Method for manufacturing steel-aluminum composite conductor rail
A technology of steel-aluminum composite and manufacturing method, which is applied in the field of conductive rails, can solve the problems of stainless steel strips not tightly bonded, high investment in production equipment, complicated preparation methods, etc., and achieve high production efficiency, low manufacturing difficulty, and good wear resistance Effect
- Summary
- Abstract
- Description
- Claims
- Application Information
AI Technical Summary
Problems solved by technology
Method used
Image
Examples
Embodiment Construction
[0041] see Figure 1 to Figure 4 , the manufacturing method of steel-aluminum composite conductor rail, it comprises the steps:
[0042] a. Preparation of aluminum rail 1
[0043] The aluminum billet is hot-extruded through an extrusion machine to form an I-shaped aluminum rail 1. Grooves 11 and 12 are formed on both sides of the upper end of the aluminum rail, and the notches of the grooves are arc-shaped.
[0044] b. Prefabricated C-shaped stainless steel belt 2
[0045] The stainless steel coil is cut into long stainless steel strips, cold-bending and rolling on cold-bending equipment, and rolled by multiple rolling dies to form a C-shaped stainless steel strip 2, which includes a base 21 and extends from the base 21 to both sides. And bend down to form the first bending part 22, 22', extend from the first bending part 22, 22' and bend inward to form the second bending part 23, 23', extend from the second bending part to form a hook Part 24, 24'; after the rolling is com...
PUM
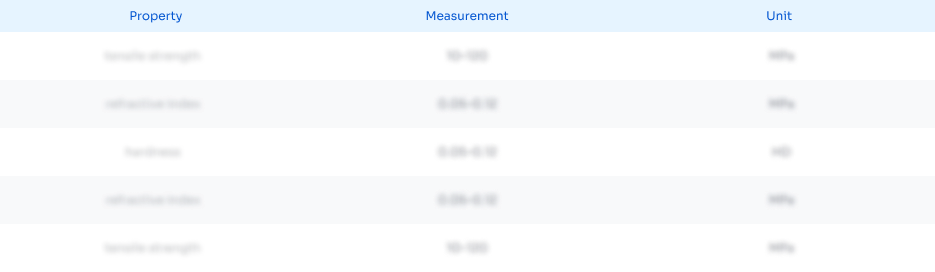
Abstract
Description
Claims
Application Information

- Generate Ideas
- Intellectual Property
- Life Sciences
- Materials
- Tech Scout
- Unparalleled Data Quality
- Higher Quality Content
- 60% Fewer Hallucinations
Browse by: Latest US Patents, China's latest patents, Technical Efficacy Thesaurus, Application Domain, Technology Topic, Popular Technical Reports.
© 2025 PatSnap. All rights reserved.Legal|Privacy policy|Modern Slavery Act Transparency Statement|Sitemap|About US| Contact US: help@patsnap.com