Temperature control rubber groove suitable for optic fiber gyroscope winding machine
A fiber optic gyroscope and loop winding machine technology, which is applied in the field of constant temperature control devices, can solve the problems of precise arrangement requirements of fiber jumpers, uneven winding of fiber loops, affecting quality and performance, etc., and achieves arbitrary adjustable position, constant temperature and high precision , cost reduction and application effect
- Summary
- Abstract
- Description
- Claims
- Application Information
AI Technical Summary
Problems solved by technology
Method used
Image
Examples
Embodiment Construction
[0035] The technical solutions in the present invention will be clearly and completely described below in conjunction with specific embodiments. Apparently, the described embodiments are only some of the embodiments of the present invention, not all of them. Based on the embodiments of the present invention, all other embodiments obtained by persons of ordinary skill in the art without making creative efforts belong to the protection scope of the present invention.
[0036] The embodiments of the present invention are further described in detail below.
[0037] The embodiment of the present invention provides a temperature-controlled glue tank suitable for an optical fiber gyro winding machine, which can accurately control the constant temperature control of the coating process. Since the temperature value can be adjusted, it can adapt to the physical properties of various glues and other fillings Changes and changes in various winding process conditions. Such as figure 1 , ...
PUM
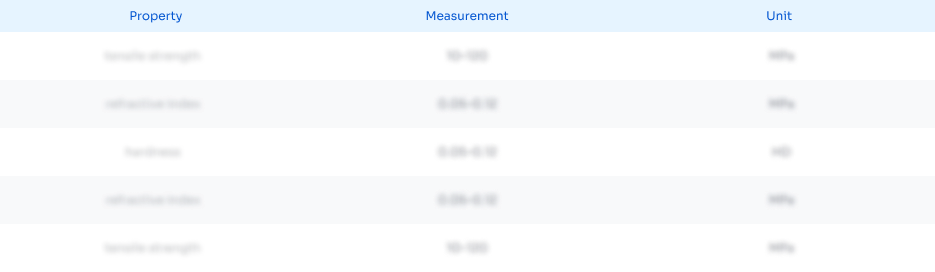
Abstract
Description
Claims
Application Information

- R&D Engineer
- R&D Manager
- IP Professional
- Industry Leading Data Capabilities
- Powerful AI technology
- Patent DNA Extraction
Browse by: Latest US Patents, China's latest patents, Technical Efficacy Thesaurus, Application Domain, Technology Topic, Popular Technical Reports.
© 2024 PatSnap. All rights reserved.Legal|Privacy policy|Modern Slavery Act Transparency Statement|Sitemap|About US| Contact US: help@patsnap.com