Manufacturing process of oil outlet tray of gasoline pump and structure of oil outlet tray
A manufacturing process and oil outlet pan technology, applied in the direction of coating, etc., can solve the problems affecting mass production quality, inconsistent coaxiality between inner bushing and disc body, inconsistent gasoline pump flow, etc.
- Summary
- Abstract
- Description
- Claims
- Application Information
AI Technical Summary
Problems solved by technology
Method used
Image
Examples
Embodiment 1
[0031] The manufacturing process of the gasoline pump oil outlet plate is to integrally form the plate body 501 and the inner liner 503 in a mold, including the following steps:
[0032] 1. Baking of raw materials, wherein the raw material used is PPS, the baking temperature is 110-125°C, preferably 110°C, and the baking time is 3.5-4.3 hours, preferably 3.5 hours.
[0033] 2. Injection molding. The steps are as follows:
[0034] (1) Mold opening, wherein, mold opening includes three stages, followed by slow mold opening, fast mold opening and deceleration mold opening; the pressure of slow mold opening is 42~45 N, and 42N is selected in this embodiment , the speed is 25~28 m / s, preferably 25m / s; the pressure of rapid mold opening is 22~26 N, preferably 22N, the speed of rapid mold opening is 28~32 m / s, preferably 28m / s; slow down mold opening The pressure is 15~17 N, preferably 15N, and the speed is 10~13 m / s, preferably 10m / s.
[0035] (2) Put the inner bushing 503 into t...
Embodiment 2
[0043] The manufacturing process of the gasoline pump oil outlet plate is to integrally form the plate body 501 and the inner liner 503 in a mold, including the following steps:
[0044] 1. Baking of raw materials, wherein the raw material used is PPS, the baking temperature is 110-125°C, preferably 125°C, and the baking time is 3.5-4.3 hours, preferably 4.3 hours.
[0045] 2. Injection molding. The steps are as follows:
[0046](1) Mold opening, wherein, mold opening includes three stages, followed by slow mold opening, fast mold opening and deceleration mold opening; the pressure of slow mold opening is 42~45 N, and 45N is selected in this embodiment , the speed is 25~28 m / s, preferably 28m / s; the pressure of rapid mold opening is 22~26 N, preferably 26N, the speed of rapid mold opening is 28~32 m / s, preferably 32m / s; slow down mold opening The pressure is 15~17 N, preferably 17N, and the speed is 10~13 m / s, preferably 13m / s.
[0047] (2) Put the inner bushing 503 into th...
Embodiment 3
[0055] The manufacturing process of the gasoline pump oil outlet plate is to integrally form the plate body 501 and the inner liner 503 in a mold, including the following steps:
[0056] 1. Baking of raw materials, wherein the selected raw material is PPS, the baking temperature is 110-125°C, preferably 120°C, and the baking time is 3.5-4.3 hours, preferably 4 hours.
[0057] 2. Injection molding. The steps are as follows:
[0058] (1) Mold opening, wherein, mold opening includes three stages, followed by slow mold opening, fast mold opening and deceleration mold opening; the pressure of slow mold opening is 42~45 N, and 43N is selected in this embodiment , the speed is 25~28 m / s, preferably 27m / s; the pressure of rapid mold opening is 22~26 N, preferably 24N, the speed of rapid mold opening is 28~32 m / s, preferably 30m / s; slow down mold opening The pressure is 15~17 N, preferably 16N, and the speed is 10~13 m / s, preferably 12m / s.
[0059] (2) Put the inner bushing 503 into...
PUM
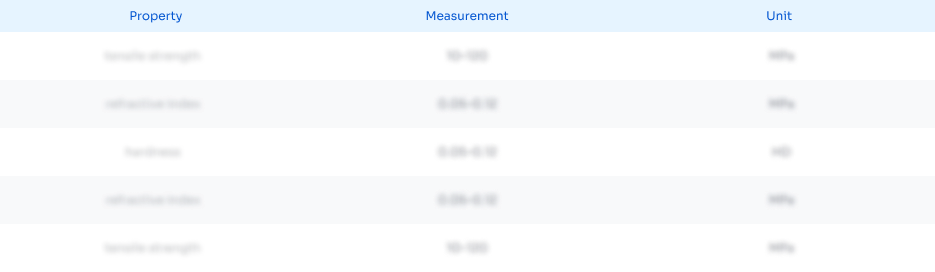
Abstract
Description
Claims
Application Information

- R&D
- Intellectual Property
- Life Sciences
- Materials
- Tech Scout
- Unparalleled Data Quality
- Higher Quality Content
- 60% Fewer Hallucinations
Browse by: Latest US Patents, China's latest patents, Technical Efficacy Thesaurus, Application Domain, Technology Topic, Popular Technical Reports.
© 2025 PatSnap. All rights reserved.Legal|Privacy policy|Modern Slavery Act Transparency Statement|Sitemap|About US| Contact US: help@patsnap.com