Method and detection sensor for detecting optical fiber grating vibration of large-scale mechanized equipment
A fiber grating and large-scale machinery technology, applied in the field of sensors, can solve problems such as poor frequency dynamic response characteristics, obstacles to the application of rotating machinery, and inability to apply high-frequency measurement, etc., to achieve fast dynamic response, eliminate influence, and anti-electromagnetic interference. strong effect
- Summary
- Abstract
- Description
- Claims
- Application Information
AI Technical Summary
Problems solved by technology
Method used
Image
Examples
Embodiment Construction
[0022] The present invention will be described in further detail below in conjunction with the accompanying drawings.
[0023] The overall installation structure of the non-contact fiber grating dynamic detection sensor: the two ends of the fiber grating 2 are respectively glued into the first capillary steel pipe 3 and the second capillary steel pipe 4, wherein the first capillary steel pipe 3 is connected to one end of the metal sleeve 5, The second capillary steel pipe 4 is connected to the central hard core of the metal diaphragm 6, and the metal diaphragm 6 is welded to the other end of the metal sleeve 5. During the installation process, the fiber grating 2 is pre-tightened, and the first magnet 8-b and The second magnet 8-c is a U-shaped sensing probe formed by connecting the soft iron 8-a—the magnetic coupling sensing probe 8, and the magnetic coupling sensing probe 8 is connected to the central hard core of the metal diaphragm 6 through the connecting rod 7 , which co...
PUM
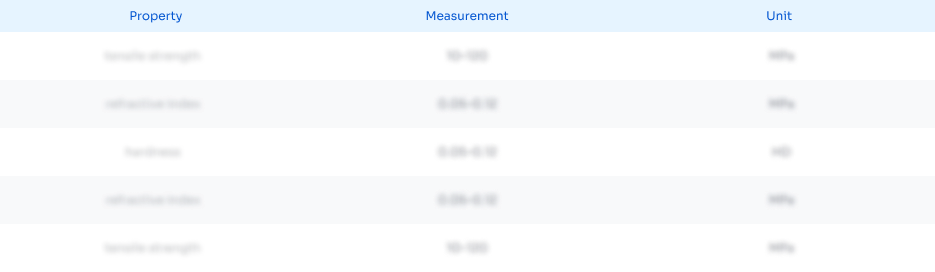
Abstract
Description
Claims
Application Information

- R&D Engineer
- R&D Manager
- IP Professional
- Industry Leading Data Capabilities
- Powerful AI technology
- Patent DNA Extraction
Browse by: Latest US Patents, China's latest patents, Technical Efficacy Thesaurus, Application Domain, Technology Topic.
© 2024 PatSnap. All rights reserved.Legal|Privacy policy|Modern Slavery Act Transparency Statement|Sitemap