Post-cure of molded polyurethane foam products
A post-curing, foaming technology, applied in the field after post-curing and before extruding foam products, can solve the problem of time-consuming post-curing operation
- Summary
- Abstract
- Description
- Claims
- Application Information
AI Technical Summary
Problems solved by technology
Method used
Image
Examples
Embodiment Construction
[0021] With reference to the drawings in general, and in particular to Figure 4 , the method for making a molded polyurethane foam article of the present disclosure includes a post-curing step 20 after demoulding 11 and before extrusion 40 . Additionally, the foam article is cooled 30 prior to extrusion 40 . Unless otherwise indicated, the disclosed methods may be performed in conventional manner and include well known materials and methods. As used herein, "foam article" is a broad term that may include - but is not limited to - slabstock foam, automotive foam (such as, for example, seat cushions, head rests, back cushions, armrests, etc.), furniture seating products, and industrial foams (eg, engine mounts, compressors, etc.).
[0022] The post-curing step 20 is performed as soon as possible after demolding 11 so that the core temperature of the polyurethane article remains elevated to reduce / shorten the time and energy required to perform the post-curing operation. Prefe...
PUM
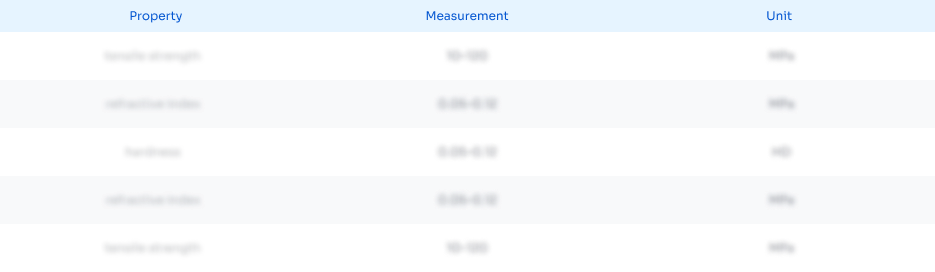
Abstract
Description
Claims
Application Information

- R&D
- Intellectual Property
- Life Sciences
- Materials
- Tech Scout
- Unparalleled Data Quality
- Higher Quality Content
- 60% Fewer Hallucinations
Browse by: Latest US Patents, China's latest patents, Technical Efficacy Thesaurus, Application Domain, Technology Topic, Popular Technical Reports.
© 2025 PatSnap. All rights reserved.Legal|Privacy policy|Modern Slavery Act Transparency Statement|Sitemap|About US| Contact US: help@patsnap.com