Method for purifying polysilicon by using silicon and tin alloy
A polysilicon and alloy technology, which is applied in the field of purifying polysilicon by using silicon-tin alloy, can solve the problem of no separation, etc., and achieve the effects of convenient operation, fast start-up, and small initial investment.
- Summary
- Abstract
- Description
- Claims
- Application Information
AI Technical Summary
Problems solved by technology
Method used
Examples
Embodiment 1
[0017] 1) Mix industrial silicon and tin powder in a mass ratio of 9:1 and put them into a graphite crucible. When charging, first fill the bottom of the crucible with silicon material, then put tin powder in, and then fill the upper part with silicon material;
[0018] 2) Put the graphite crucible into the directional solidification furnace, then evacuate the solidification furnace, control the vacuum degree to 0.5Pa, raise the temperature in the furnace to 1480°C within 2.5 hours, melt the industrial silicon and tin powder in the graphite crucible, When the temperature rises to 100°C, a pre-prepared protective gas with a suitable ratio is introduced: Ar (99.999%) + water vapor (2ppm) + O 2 (1ppm)+N 2 (4ppm), to normal pressure;
[0019] 3) Insulate the fused industrial silicon and tin powder in step 2) for 3 hours to ensure that it fully melts and melts with silicon and tin melt to form an alloy;
[0020] 4) Cool the alloy in step 3) to 1200°C at a cooling rate of 10°C / h u...
Embodiment 2
[0023]Raw material and technological process are with embodiment 1. The amount of tin powder added is 20%, the vacuum degree in the directional solidification furnace is 0.6Pa, the melting temperature is 1490°C, and the heating time is 3h. When the temperature rises to 200°C, gas is introduced. The holding time at the melting temperature is 3.5h. When cooling and solidifying, the temperature drops to 1250°C, and the cooling rate is 20°C / h. The lower 10% of the obtained alloy silicon ingot is cut off and passed through a plasma inductively coupled mass spectrometer (ICP-MS). ) measured the P content in this polysilicon to be 0.08ppmw, the B content to be 0.3ppmw, and the purity of the polysilicon to be 99.99937%.
Embodiment 3
[0025] Raw material and technological process are with embodiment 1. The amount of tin powder added is 30%, the vacuum degree in the directional solidification furnace is 0.7Pa, the melting temperature is 1580°C, and the heating time is 4.5h. When the temperature rises to 300°C, gas is introduced. The holding time at the melting temperature is 5h. When cooling and solidifying, the temperature drops to 1300°C, and the cooling rate is 30°C / h. The lower 20% of the obtained alloy silicon ingot is cut off and passed through a plasma inductively coupled mass spectrometer (ICP-MS). It was determined that the P content in the polysilicon was 0.05 ppmw, the B content was 0.4 ppmw, and the purity of the polysilicon was 99.99942%.
PUM
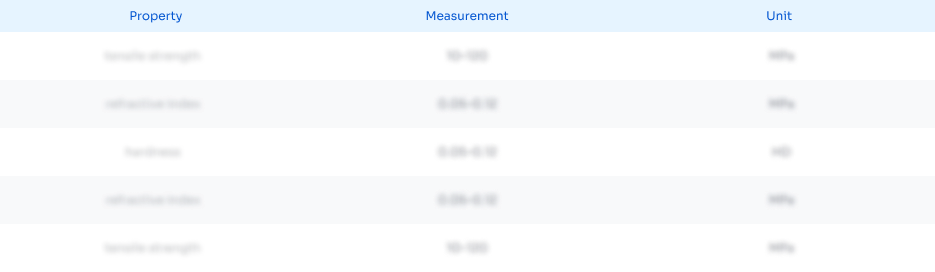
Abstract
Description
Claims
Application Information

- R&D
- Intellectual Property
- Life Sciences
- Materials
- Tech Scout
- Unparalleled Data Quality
- Higher Quality Content
- 60% Fewer Hallucinations
Browse by: Latest US Patents, China's latest patents, Technical Efficacy Thesaurus, Application Domain, Technology Topic, Popular Technical Reports.
© 2025 PatSnap. All rights reserved.Legal|Privacy policy|Modern Slavery Act Transparency Statement|Sitemap|About US| Contact US: help@patsnap.com