Hot press
A technology of hot press and pressing plate, which is applied in lamination, lamination device, layered products, etc. It can solve problems such as inconsistent surface temperature of pressing plate, carbonization of plate surface temperature, insufficient thermal processing, etc., so as to avoid product defects and save Electric energy, the effect of improving the effect of thermal processing and forming
- Summary
- Abstract
- Description
- Claims
- Application Information
AI Technical Summary
Problems solved by technology
Method used
Image
Examples
Embodiment Construction
[0009] As shown in Figure 1, the lower platen 3 of the hot press is supported on the base 4, the upper platen 2 is fixed below the cylinder 1, and a plurality of electric heating tubes 5 are installed on the upper and lower platens 2,3.
[0010] The upper and lower platens 2, 3 are provided with heat conduction oil passages, and the heat conduction oil passages are arranged in the area between the pressing surfaces 23, 33 of the upper and lower platens 2, 3 and the electric heating tube 5. figure 2 Shown is the heat conduction oil circuit structure of the lower platen 3. The heat conduction oil route is composed of a parallel longitudinal channel 36 and a horizontal channel 35 connecting two adjacent longitudinal channels. The longitudinal channel 36 is formed by a through hole processed on one side of the platen 3. Both ends of the hole are provided with a cover 34, and a horizontal passage 35 is located inside the cover 33. The longitudinal passages on both sides of the pres...
PUM
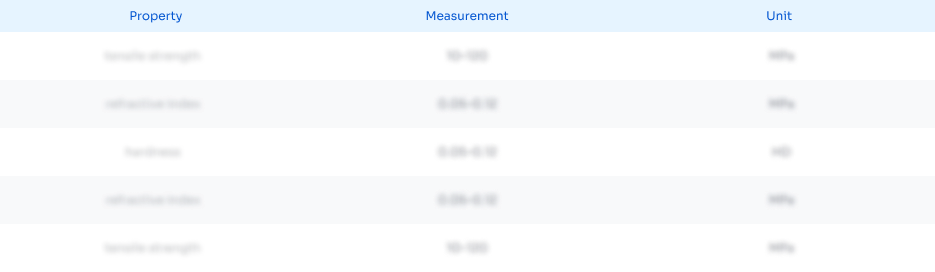
Abstract
Description
Claims
Application Information

- R&D Engineer
- R&D Manager
- IP Professional
- Industry Leading Data Capabilities
- Powerful AI technology
- Patent DNA Extraction
Browse by: Latest US Patents, China's latest patents, Technical Efficacy Thesaurus, Application Domain, Technology Topic, Popular Technical Reports.
© 2024 PatSnap. All rights reserved.Legal|Privacy policy|Modern Slavery Act Transparency Statement|Sitemap|About US| Contact US: help@patsnap.com