Anti-shaking control method for container shore bridge hanger
A control method and container technology, applied in the directions of transportation and packaging, load hoisting elements, etc., can solve the problems of large influence of anti-sway control, reduced operator comfort, frequent operation, etc., to avoid frequent adjustment and improve automatic operation. Horizontal, easy-to-debug effects
- Summary
- Abstract
- Description
- Claims
- Application Information
AI Technical Summary
Problems solved by technology
Method used
Image
Examples
Embodiment Construction
[0024] The first embodiment of the method of the present invention is used for the whole process control of trolley operation, such as figure 1 As shown, the anti-sway control system that implements the anti-sway control method shares five signals that need to be measured: trolley speed, spreader lifting speed, trolley position, spreader pendulum length and spreader swing angle. Walking absolute rotary encoders, lifting absolute rotary encoders and machine vision sensors composed of smart cameras, reflectors, etc. are measured, and are transmitted to the anti-sway controller through the field bus for algorithm calculation and control. Due to the introduction of sensors for hoisting With real-time measurement of the swing angle, the anti-sway control effect is improved, and it is not affected by the initial state of the heavy object, and the influence of factors such as wind force can also be compensated. The machine vision sensor is composed of a smart camera 5 installed at t...
PUM
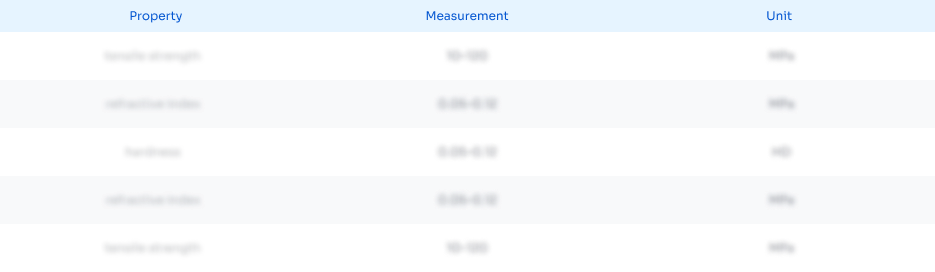
Abstract
Description
Claims
Application Information

- Generate Ideas
- Intellectual Property
- Life Sciences
- Materials
- Tech Scout
- Unparalleled Data Quality
- Higher Quality Content
- 60% Fewer Hallucinations
Browse by: Latest US Patents, China's latest patents, Technical Efficacy Thesaurus, Application Domain, Technology Topic, Popular Technical Reports.
© 2025 PatSnap. All rights reserved.Legal|Privacy policy|Modern Slavery Act Transparency Statement|Sitemap|About US| Contact US: help@patsnap.com