Automatic calibration apparatus for robot tool coordinate system based on laser tracking measurement and method thereof
A technology of laser tracking measurement and tool coordinate system, which is applied in the direction of measuring devices, optical devices, instruments, etc., can solve the problems of cumbersome robot tool coordinate system, complicated operation, and not given, and achieve good application scalability, operation and The effect of simple control process and high reliability
- Summary
- Abstract
- Description
- Claims
- Application Information
AI Technical Summary
Problems solved by technology
Method used
Image
Examples
Embodiment Construction
[0045] like figure 1 As shown, the robot tool coordinate system automatic calibration device based on laser tracking measurement includes a robot 1, a target flange 2, a target mounting hole 3, a laser tracker 4, a tool 5, and a host computer 6; the robot 1 is equipped with a target flange 2 , tool 5, six target mounting holes 3 on the target flange 2, a laser tracker 4 and a host computer 6 on the outer side of the robot 1.
[0046] The calibration error of the robot 1 is reduced to 0.103657mm.
[0047] Between described upper computer 6, robot 1, laser tracker 4, realize Socket communication through RS485 ethernet connection, send data, order, request with the form of character string, finish the backup and the backup of measurement data and calculation data by upper computer 6 save.
[0048] The steps of calibrating the robot tool coordinate system 9 are as follows:
[0049] 1) Robot 1 returns to the mechanical origin, records the current position through robot 1, and ma...
PUM
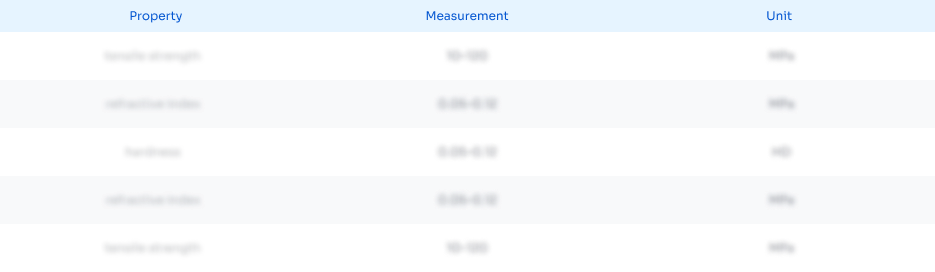
Abstract
Description
Claims
Application Information

- Generate Ideas
- Intellectual Property
- Life Sciences
- Materials
- Tech Scout
- Unparalleled Data Quality
- Higher Quality Content
- 60% Fewer Hallucinations
Browse by: Latest US Patents, China's latest patents, Technical Efficacy Thesaurus, Application Domain, Technology Topic, Popular Technical Reports.
© 2025 PatSnap. All rights reserved.Legal|Privacy policy|Modern Slavery Act Transparency Statement|Sitemap|About US| Contact US: help@patsnap.com