Positive and negative helical focusing mechanism
An anti-screw, positive and negative technology, applied in the field of aerospace focusing, can solve the problems of poor structural stability and large structural voids, and achieve the effects of reducing shaking, increasing stability, and improving the uniformity of force
- Summary
- Abstract
- Description
- Claims
- Application Information
AI Technical Summary
Problems solved by technology
Method used
Image
Examples
Embodiment Construction
[0012] The specific implementation manners of the present invention will be described in detail below in conjunction with the accompanying drawings.
[0013] Depend on figure 1 , 2 As shown, the positive and negative spiral focusing mechanism is characterized in that it includes a mirror 1, a mirror back plate support structure, a bottom plate structure, a guide rod structure, a positive and negative screw screw structure, two connecting rods 8, and a stepping motor 6 and the multi-turn absolute encoder 7, the reflector 1 is installed on the support structure of the reflector back plate, the support structure of the reflector back plate is installed on the base plate structure, the positive and negative screw screw structure is installed on the lower part of the base plate structure, and one end of it is connected to the step The motor 6 is connected, the other end is connected with the multi-turn absolute encoder 7, and the middle part of the positive and negative screw scre...
PUM
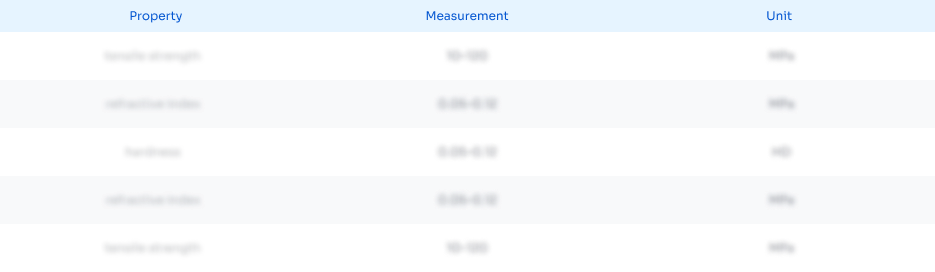
Abstract
Description
Claims
Application Information

- Generate Ideas
- Intellectual Property
- Life Sciences
- Materials
- Tech Scout
- Unparalleled Data Quality
- Higher Quality Content
- 60% Fewer Hallucinations
Browse by: Latest US Patents, China's latest patents, Technical Efficacy Thesaurus, Application Domain, Technology Topic, Popular Technical Reports.
© 2025 PatSnap. All rights reserved.Legal|Privacy policy|Modern Slavery Act Transparency Statement|Sitemap|About US| Contact US: help@patsnap.com