Shaping system for integrally cutting, crimping and pressing edge
A technology of edge pressing and trimming, which is applied to other manufacturing equipment/tools, manufacturing tools, etc., can solve the problems of inconsistent plastic quality and low work efficiency, and achieve the effects of reducing production costs, improving production efficiency and plastic quality
- Summary
- Abstract
- Description
- Claims
- Application Information
AI Technical Summary
Problems solved by technology
Method used
Image
Examples
Embodiment Construction
[0012] The present invention will be described in detail below in conjunction with the accompanying drawings and specific embodiments.
[0013] The schematic diagram of the trimming, crimping and trimming integrated shaping system of the present invention is as follows figure 1 and figure 2 Shown, comprise main frame 17, bucket hanger frame 6, bucket tray 10, bucket rotating motor 15, platen 5, platen lifting drive mechanism, trimming mechanism, crimping mechanism and crimping mechanism. On the main frame 17, a bucket stand 6 is installed, and on the main frame 17, a trimming mechanism, a crimping mechanism and a crimping mechanism are respectively arranged at positions corresponding to the bung. The edge trimming mechanism includes an edge trimming tool advancing and retreating drive mechanism installed on the main frame, and the edge trimming tool advancing and retreating driving mechanism is connected with an edge trimming tool holder 12 on which an edge trimming tool 11 ...
PUM
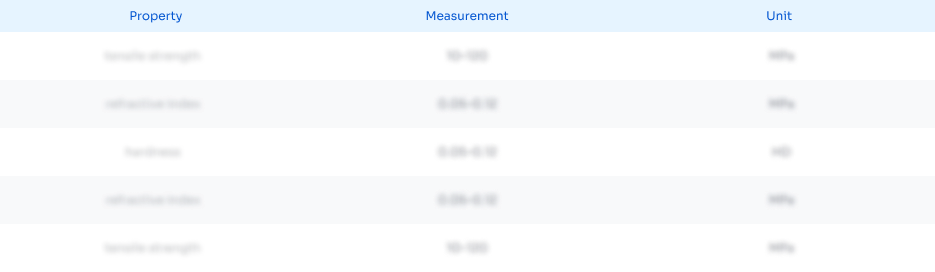
Abstract
Description
Claims
Application Information

- Generate Ideas
- Intellectual Property
- Life Sciences
- Materials
- Tech Scout
- Unparalleled Data Quality
- Higher Quality Content
- 60% Fewer Hallucinations
Browse by: Latest US Patents, China's latest patents, Technical Efficacy Thesaurus, Application Domain, Technology Topic, Popular Technical Reports.
© 2025 PatSnap. All rights reserved.Legal|Privacy policy|Modern Slavery Act Transparency Statement|Sitemap|About US| Contact US: help@patsnap.com