Method for changing a roller in a roll mill for a continuously running steel strip
A technology of traveling direction and rolling mill, applied in the direction of metal rolling stand, metal rolling mill stand, rolling force/roll gap control, etc., can solve the problems of aggravation, incorrect control of replacement operation, etc., and achieve time sequence simplification, Effect of good scrap recycling, time sequence reduction
- Summary
- Abstract
- Description
- Claims
- Application Information
AI Technical Summary
Problems solved by technology
Method used
Image
Examples
Embodiment Construction
[0044] All the figures described below show a rolling mill comprising six stands and their rolls C1 , C2 , C3 , C4 , C5 , C6 arranged one behind the other in the direction D of their travel along the continuously running strip B. For the sake of clarity, the upper section of the strip, interrupted by the plane of symmetry Ax (parallel and equidistant to the two surfaces of the strip) is also shown. A clamp command value R1, R2, R3, R4, R5 is assigned to each of the five rolls in the rolling working position among the six rolls. By extension, the term "frame" will be used to denote at least one roller in the frame. Likewise, the terms "first rack", "second rack" ... "Nth rack" will be used. This number indicates that the first stand is located furthest upstream in the direction D of strip travel (at the strip entry to the rolling mill), while subsequent stands are placed more and more downstream of the first stand.
[0045] More generally, the rolling mill shown allows implem...
PUM
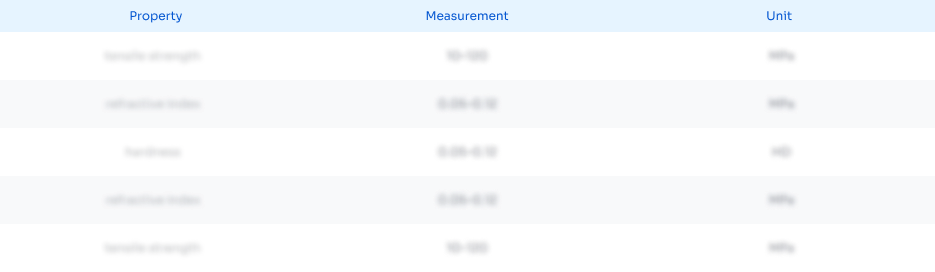
Abstract
Description
Claims
Application Information

- R&D
- Intellectual Property
- Life Sciences
- Materials
- Tech Scout
- Unparalleled Data Quality
- Higher Quality Content
- 60% Fewer Hallucinations
Browse by: Latest US Patents, China's latest patents, Technical Efficacy Thesaurus, Application Domain, Technology Topic, Popular Technical Reports.
© 2025 PatSnap. All rights reserved.Legal|Privacy policy|Modern Slavery Act Transparency Statement|Sitemap|About US| Contact US: help@patsnap.com