Fatigue test device of rubber bearing
A fatigue test, rubber bearing technology, applied in the direction of mechanical bearing testing, etc., can solve the problem of low rigidity of the fixture
- Summary
- Abstract
- Description
- Claims
- Application Information
AI Technical Summary
Problems solved by technology
Method used
Image
Examples
Embodiment Construction
[0016] The technical solutions of the present invention will be further described below in conjunction with the accompanying drawings and embodiments.
[0017] see image 3 , Figure 4 The fatigue test device 10 of the rubber bearing shown is set on the test platform of the test device, including a clamping mechanism 11, a pair of bearing seats 12 provided with a rotating mandrel 121, and a swing rod 13, and the bearing seats 12 are arranged symmetrically on the clamp. The two ends of tight mechanism 11, fork 13 are connected with the outer end of a bearing seat 12. The clamping mechanism 11 includes flanges 111 and fastening parts 112, the flanges 111 are respectively arranged on the inner ends of the bearing housing 12, and the fastening parts 112 are arranged between the flanges 111 and connected with the flanges 111 fixed. Since the flange is circular and the stiffness is isotropic, the rigidity of the clamping mechanism 11 in the direction of tension and pressure is al...
PUM
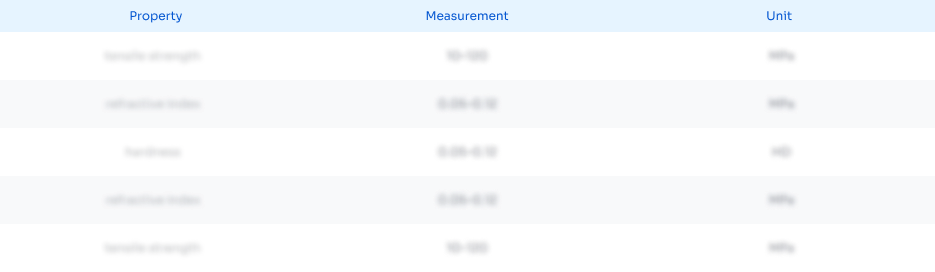
Abstract
Description
Claims
Application Information

- R&D
- Intellectual Property
- Life Sciences
- Materials
- Tech Scout
- Unparalleled Data Quality
- Higher Quality Content
- 60% Fewer Hallucinations
Browse by: Latest US Patents, China's latest patents, Technical Efficacy Thesaurus, Application Domain, Technology Topic, Popular Technical Reports.
© 2025 PatSnap. All rights reserved.Legal|Privacy policy|Modern Slavery Act Transparency Statement|Sitemap|About US| Contact US: help@patsnap.com