System for generating low-pressure steam by utilizing flue gas waste heat
A flue gas waste heat and low-pressure steam technology, which is applied in the system field of using flue gas waste heat to generate low-pressure steam, can solve the problems of different process requirements and difficulty in generating low-pressure steam, and achieve the effect of reducing the exhaust gas temperature
- Summary
- Abstract
- Description
- Claims
- Application Information
AI Technical Summary
Problems solved by technology
Method used
Image
Examples
Embodiment Construction
[0016] A system for generating low-pressure steam by utilizing flue gas waste heat of the present invention includes a boiler flue 4 with multi-stage heating surfaces, wherein the last-stage heating surface is located at the tail of the boiler flue. In the following two specific embodiments, the last-stage The heating surface refers to the air preheater 3 and the second-stage air preheater respectively, and also includes the flue gas waste heat evaporator 2 and the flue gas waste heat recovery and utilization device. The flue gas waste heat evaporator 2 is added to the final stage of the boiler flue 4 Before the heating surface, the flue gas waste heat recovery and utilization device includes a connected heat absorption section 5 and a heat release section 7, and the heat absorption section 5 is added behind the final stage heating surface in the boiler flue. There is also a dust removal and desulfurization device in the boiler flue behind the final heating surface, and the hea...
PUM
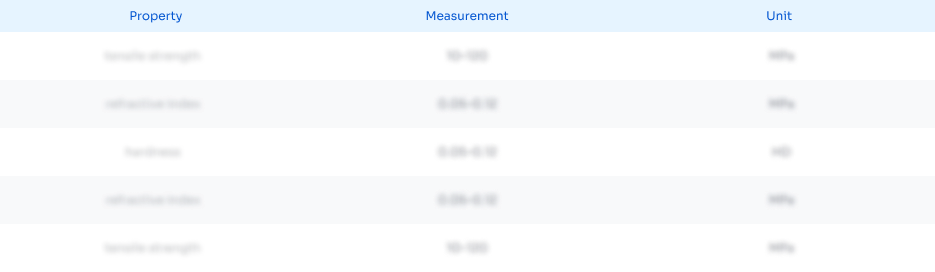
Abstract
Description
Claims
Application Information

- R&D
- Intellectual Property
- Life Sciences
- Materials
- Tech Scout
- Unparalleled Data Quality
- Higher Quality Content
- 60% Fewer Hallucinations
Browse by: Latest US Patents, China's latest patents, Technical Efficacy Thesaurus, Application Domain, Technology Topic, Popular Technical Reports.
© 2025 PatSnap. All rights reserved.Legal|Privacy policy|Modern Slavery Act Transparency Statement|Sitemap|About US| Contact US: help@patsnap.com