Energy-saving speed-regulating permanent magnet driver
A drive and permanent magnet technology, applied in the field of drives, can solve problems such as no buffer starting device, motor stalling, affecting work progress, etc., to achieve soft start, reduce vibration, and solve the effects of stalling
- Summary
- Abstract
- Description
- Claims
- Application Information
AI Technical Summary
Problems solved by technology
Method used
Image
Examples
Embodiment Construction
[0010] An energy-saving speed-regulating permanent magnet driver, comprising a speed-regulating device 10, the speed-regulating device 10 is arranged along the axial direction of a motor shaft 90 and a load shaft 20, the motor shaft 90 and the load shaft 20 are on the same central axis, the motor shaft 90 There is a gap between it and the load shaft 20. The speed regulating device 10 includes a copper rotor 30, a permanent magnet rotor 40 and a controller 50. The copper rotor 30 is fixed on the load shaft 20, and the permanent magnet rotor 40 is fixed on the motor through a bracket 60. The copper There is an air gap 80 between the rotor 30 and the permanent magnet rotor 40, such as figure 1 shown.
[0011] Such as figure 1 As shown, the load shaft 20 is also provided with a base 70 for supporting the load shaft 20, the base 70 is provided with a through hole for the load shaft 20 to pass through, the base 70 is provided with a copper sleeve 71, the base 70 70 is fixedly conn...
PUM
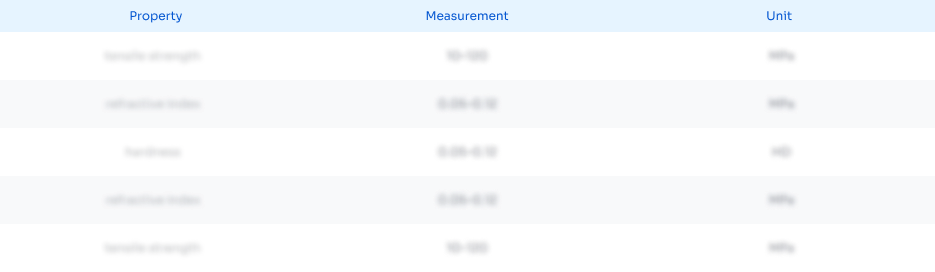
Abstract
Description
Claims
Application Information

- R&D
- Intellectual Property
- Life Sciences
- Materials
- Tech Scout
- Unparalleled Data Quality
- Higher Quality Content
- 60% Fewer Hallucinations
Browse by: Latest US Patents, China's latest patents, Technical Efficacy Thesaurus, Application Domain, Technology Topic, Popular Technical Reports.
© 2025 PatSnap. All rights reserved.Legal|Privacy policy|Modern Slavery Act Transparency Statement|Sitemap|About US| Contact US: help@patsnap.com