Conductive ink and preparation method thereof
A technology of conductive ink and acrylic resin, which is applied in the field of copper-doped conductive ink and its preparation, can solve the problems of reducing the conductivity of slurry and other physical properties, poor anti-aging, and affecting product performance, achieving long-lasting performance, It is not easy to oxidize and does not affect the quality of the effect
- Summary
- Abstract
- Description
- Claims
- Application Information
AI Technical Summary
Problems solved by technology
Method used
Examples
Example Embodiment
[0024] Example 1
[0025] The preparation of conductive ink is specifically:
[0026] 1) In terms of parts by mass, mix 65 parts of 1,4-butyrolactone with 35 parts of vinyl acetate resin, and stir (500 rpm) for 5 hours in a 70°C water bath to dissolve the vinyl acetate resin , Get the organic carrier A;
[0027] Mix 65 parts of diethyl adipate and 35 parts of epoxy acrylic resin, and place them in a 70°C water bath and stir (500 revolutions / min) for 5 hours to dissolve the epoxy acrylic resin to obtain an organic carrier B;
[0028] 2) Weigh according to the following mass parts:
[0029] 50 parts of flake silver powder with an average particle size of 5-20 microns;
[0030] 6 parts of silver-coated copper powder with spherical shape and average particle size not exceeding 5 microns, in which the mass ratio of silver to copper is 1:5;
[0031] 40 parts of organic carrier A;
[0032] 3.85 parts of organic carrier B;
[0033] 0.15 parts of KH-550 as coupling agent;
[0034] According to the a...
Example Embodiment
[0035] Example 2
[0036] The preparation of conductive ink is specifically:
[0037] 1) In parts by mass, mix 60 parts of isophorone with 40 parts of chloroacetate resin, and place in a water bath at 100°C and stir (600 rpm) for 2 hours to dissolve the chloroacetate resin to obtain organic Carrier A;
[0038] Mix 65 parts of diethyl adipate with 35 parts of thermosetting acrylic resin, and stir (600 rpm) for 2 hours in a 100°C water bath to dissolve the thermosetting acrylic resin to obtain an organic carrier B;
[0039] 2) Weigh according to the following mass parts:
[0040] 40 parts of flake silver powder with an average particle size of 5-20 microns;
[0041] 10 parts of spherical silver-coated copper powder with an average particle size not exceeding 5 microns; the mass ratio of silver to copper is 1:10;
[0042] 45 parts of organic carrier A;
[0043] 4.85 copies of organic carrier B;
[0044] 0.15 parts of KH-550 as coupling agent;
[0045] According to the above mass ratio, fully m...
Example Embodiment
[0046] Example 3
[0047] The preparation of conductive ink is specifically:
[0048] 1) In terms of parts by mass, mix 65 parts of 1,4-butyrolactone with 35 parts of vinyl acetate resin, and stir (800 rpm) for 3 hours in a water bath at 80°C to dissolve the vinyl acetate resin , Get the organic carrier A;
[0049] Mix 75 parts of ethylene glycol butyl ether acetate with 25 parts of epoxy acrylic resin, and place it in a water bath at 80° C. and stir (800 rpm) for 3 hours to dissolve the epoxy acrylic resin to obtain an organic carrier B;
[0050] 2) Weigh according to the following mass parts:
[0051] 55 parts of flake silver powder with an average particle size of 5-20 microns;
[0052] 5 parts of silver-coated copper powder with spherical shape and average particle size not exceeding 5 microns; the mass ratio of silver to copper is 1:8;
[0053] 35 parts of organic carrier A;
[0054] Organic Carrier B 4.9 parts;
[0055] 0.1 part of KH-550 as coupling agent;
[0056] According to the a...
PUM
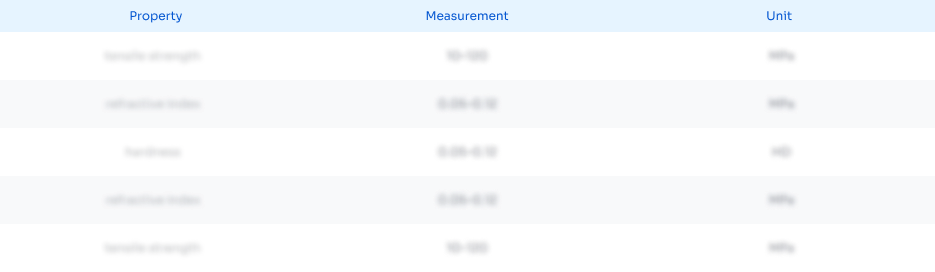
Abstract
Description
Claims
Application Information

- R&D
- Intellectual Property
- Life Sciences
- Materials
- Tech Scout
- Unparalleled Data Quality
- Higher Quality Content
- 60% Fewer Hallucinations
Browse by: Latest US Patents, China's latest patents, Technical Efficacy Thesaurus, Application Domain, Technology Topic, Popular Technical Reports.
© 2025 PatSnap. All rights reserved.Legal|Privacy policy|Modern Slavery Act Transparency Statement|Sitemap|About US| Contact US: help@patsnap.com