Stator coil and method of manufacturing the same
A technology for stator coils and manufacturing methods, which is applied in the field of wave winding stator coils and its manufacturing, which can solve the problems of wire damage, large angle, discharge of coil end 4a, etc., to reduce damage, increase floor area, and improve reliability Effect
- Summary
- Abstract
- Description
- Claims
- Application Information
AI Technical Summary
Problems solved by technology
Method used
Image
Examples
Embodiment Construction
[0034] Hereinafter, the mode for carrying out the present invention will be described in detail with reference to the drawings.
[0035] Figure 4 The perspective view which shows the stator 10 which assembled the stator coil 20 of this invention to the stator core 11. The stator core 11 is made of a magnetic material having an annular portion 12 and a plurality of teeth 13 protruding from the inner peripheral surface of the annular portion 12 toward the center of the annular portion 12 , and between the plurality of teeth 13 A plurality of slots 14 are formed for accommodating coil side portions 21 a described later of the stator coil 20 . The stator core 11 of the present embodiment represents a laminated stator core formed by laminating and fixing core plates having a predetermined thickness of annular portions 12 and teeth 13 to a predetermined thickness.
[0036] The stator coil 20 of the present invention is a coil before being assembled into the core 11, such as fig...
PUM
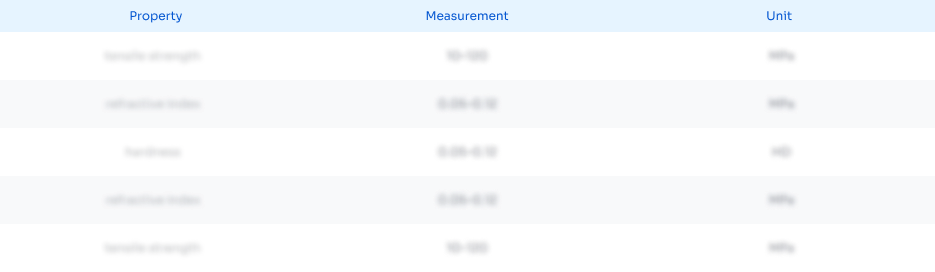
Abstract
Description
Claims
Application Information

- R&D Engineer
- R&D Manager
- IP Professional
- Industry Leading Data Capabilities
- Powerful AI technology
- Patent DNA Extraction
Browse by: Latest US Patents, China's latest patents, Technical Efficacy Thesaurus, Application Domain, Technology Topic, Popular Technical Reports.
© 2024 PatSnap. All rights reserved.Legal|Privacy policy|Modern Slavery Act Transparency Statement|Sitemap|About US| Contact US: help@patsnap.com