Method for treating waste incineration fly ash by electric melting
A waste incineration fly ash and treatment method technology, which is applied in the field of electrofusion treatment for the decomposition of dioxin and the stable solidification of heavy metals, can solve the problems of high cost, high content and difficult disposal of fly ash fusion, and achieves convenient operation, Good heat storage and heat preservation performance, high efficiency effect
- Summary
- Abstract
- Description
- Claims
- Application Information
AI Technical Summary
Problems solved by technology
Method used
Image
Examples
Embodiment 1
[0025] Such as figure 1 As shown, the fly ash, quartz sand and soda ash are uniformly mixed according to the weight ratio of 90:8:2 to obtain the mixture 1, which is put into the glass electric melting furnace 2 and fully melted at 1250-1500°C. After 8-10 hours, the electric The glass liquid level in the furnace is stable. A small amount of dust-laden flue gas 3 is produced during the melting process, which is dedusted by the bag filter 4, and the purified flue gas is discharged into the atmosphere through the induced draft fan 5 and the chimney 6.
[0026] The mixture 1 is added to the electric glass melting furnace 2 to form a high-temperature glass liquid 7, which is discharged into the water quenching system 8 from the middle of the electric glass melting furnace 2, and the glass slag 9 is obtained after quenching with cold water.
Embodiment 2
[0028] Such as figure 1 As shown, the fly ash, quartz sand and lime are uniformly mixed according to the weight ratio of 90:2:8 to obtain the mixture 1, which is put into the glass electric melting furnace 2 and fully melted at 1250-1500°C. After 8-10 hours, the mixture is The glass liquid level in the furnace is stable. A small amount of dust-laden flue gas 3 is produced during the melting process, which is dedusted by the bag filter 4, and the purified flue gas is discharged into the atmosphere through the induced draft fan 5 and the chimney 6.
[0029] The mixture 1 is added to the electric glass melting furnace 2 to form a high-temperature glass liquid 7, which is discharged into the water quenching system 8 from the middle of the electric glass melting furnace 2, and the glass slag 9 is obtained after quenching with cold water.
Embodiment 3
[0031] Such as figure 1 As shown, the fly ash, quartz sand and soda ash are uniformly mixed according to the weight ratio of 92:5:3 to obtain the mixture 1, which is put into the glass electric melting furnace 2 and fully melted at 1250-1500°C. After 8-10 hours, the electric The glass liquid level in the furnace is stable. A small amount of dust-laden flue gas 3 is produced during the melting process, which is dedusted by the bag filter 4, and the purified flue gas is discharged into the atmosphere through the induced draft fan 5 and the chimney 6.
[0032] The mixture 1 is added to the electric glass melting furnace 2 to form a high-temperature glass liquid 7, which is discharged into the water quenching system 8 from the middle of the electric glass melting furnace 2, and the glass slag 9 is obtained after quenching with cold water.
PUM
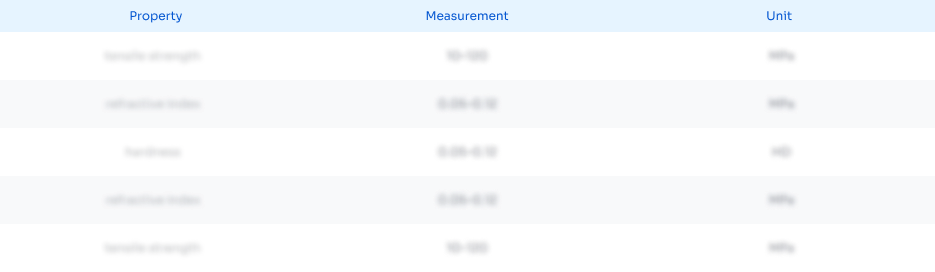
Abstract
Description
Claims
Application Information

- R&D
- Intellectual Property
- Life Sciences
- Materials
- Tech Scout
- Unparalleled Data Quality
- Higher Quality Content
- 60% Fewer Hallucinations
Browse by: Latest US Patents, China's latest patents, Technical Efficacy Thesaurus, Application Domain, Technology Topic, Popular Technical Reports.
© 2025 PatSnap. All rights reserved.Legal|Privacy policy|Modern Slavery Act Transparency Statement|Sitemap|About US| Contact US: help@patsnap.com