Method for measuring precision of 1# frame of plane general assembly
A technology of precision measurement and general assembly, applied in measurement devices, optical devices, instruments, etc., can solve the problems of inhibiting the improvement of measurement accuracy and measurement efficiency, low degree of automation, poor reliability of measurement data, etc. Improve measurement efficiency, improve measurement accuracy, and improve the effect of automation
- Summary
- Abstract
- Description
- Claims
- Application Information
AI Technical Summary
Problems solved by technology
Method used
Image
Examples
Embodiment approach
[0038] 1) Level the aircraft, that is, adjust the horizontal and longitudinal directions of the aircraft. The method is: arrange two measuring points symmetrically on the left and right wings of the aircraft. Two measurement points are arranged in the direction of the aircraft fuselage, and the height difference between the two points is within 0.5mm to achieve longitudinal leveling. Secondly, the measurement coordinate system of the laser tracker is the same as the assembly coordinate system of the aircraft general assembly station. Here, the laser The measurement coordinate system of the tracker refers to the spatial coordinate system automatically established by default after the laser tracker is turned on, while the assembly coordinate system of the aircraft general assembly site refers to the spatial coordinate system defined by the designer according to the layout of the aircraft general assembly on site. The two methods are: by measuring several public observation points...
PUM
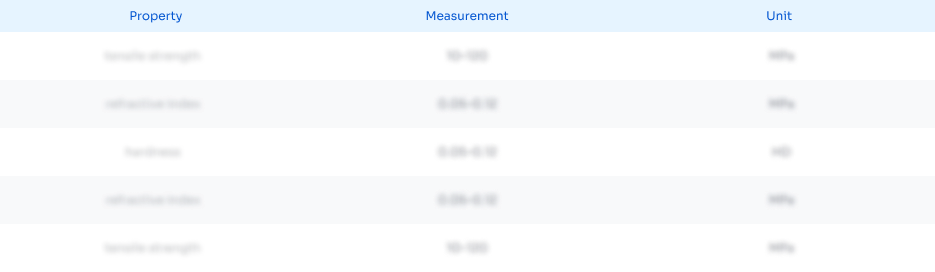
Abstract
Description
Claims
Application Information

- R&D
- Intellectual Property
- Life Sciences
- Materials
- Tech Scout
- Unparalleled Data Quality
- Higher Quality Content
- 60% Fewer Hallucinations
Browse by: Latest US Patents, China's latest patents, Technical Efficacy Thesaurus, Application Domain, Technology Topic, Popular Technical Reports.
© 2025 PatSnap. All rights reserved.Legal|Privacy policy|Modern Slavery Act Transparency Statement|Sitemap|About US| Contact US: help@patsnap.com