Initiative exhaust method for injection mould and vacuum valve device for injection mould
A technology for injection molds and vacuum valves, applied in valve devices, valve operation/release devices, valve details, etc., can solve the problem of fewer injection molds, achieve the effects of prolonging life, improving filling effect, and speeding up injection speed
- Summary
- Abstract
- Description
- Claims
- Application Information
AI Technical Summary
Problems solved by technology
Method used
Image
Examples
Embodiment Construction
[0029] The following embodiments will further describe the present invention in detail in conjunction with the accompanying drawings.
[0030] figure 1 with 2 The three-dimensional structural schematic diagram of the vacuum valve device for the injection mold described in the embodiment of the present invention assembled with the movable mold side and the partial cross-sectional view in the open state are given, Figure 4~6 The three-dimensional structure diagram of the valve core, the valve core control rod and the piston rod of the vacuum valve device for injection mold according to the embodiment of the present invention is given.
[0031] On the movable mold core 010, a circular valve hole 011 communicating with the cavity 050 is opened in the area where exhaust is required. The cavity 050 is a space formed by the movable mold core 010 and the fixed mold core 030. On the movable mold core 010, a rectangular guide hole 012 is opened perpendicular to the direction of the v...
PUM
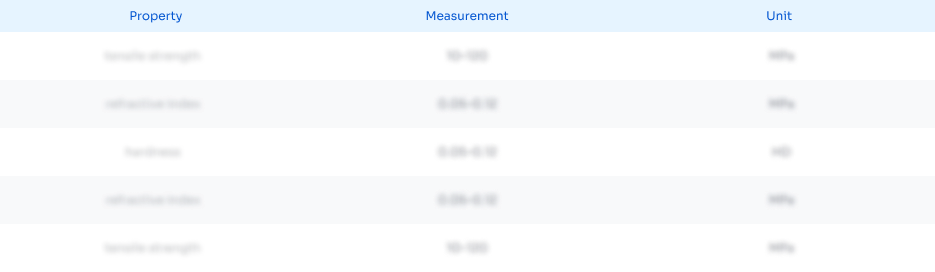
Abstract
Description
Claims
Application Information

- R&D
- Intellectual Property
- Life Sciences
- Materials
- Tech Scout
- Unparalleled Data Quality
- Higher Quality Content
- 60% Fewer Hallucinations
Browse by: Latest US Patents, China's latest patents, Technical Efficacy Thesaurus, Application Domain, Technology Topic, Popular Technical Reports.
© 2025 PatSnap. All rights reserved.Legal|Privacy policy|Modern Slavery Act Transparency Statement|Sitemap|About US| Contact US: help@patsnap.com