Command back calculation method for numerical control system
A numerical control and calculation method technology, applied in the direction of digital control, electrical program control, etc.
- Summary
- Abstract
- Description
- Claims
- Application Information
AI Technical Summary
Problems solved by technology
Method used
Image
Examples
Embodiment Construction
[0036] Relevant technical content and detailed description of the present invention, cooperate drawing description as follows:
[0037] See figure 1 It is a schematic diagram of communication between a host controller and a driver in the present invention. Taking the electrical system configuration of a CNC machine tool as an example: the host controller 10 generates a periodic position point data by a G-code interpreter (not shown). The host controller 10 is electrically connected to the driver 20 , and the host controller 10 sends a pulse wave position command to the multi-axis AC servo driver 20 . The commands between the host controller 10 and the driver 20 are transmitted through only one transmission line, which makes the wiring simple. The host controller 10 and the driver 20 respectively have a high-speed serial communication interface 102 , 202 . The generation period of a position command of the host controller 10 is T (seconds). Similarly, the driver 20 acquires...
PUM
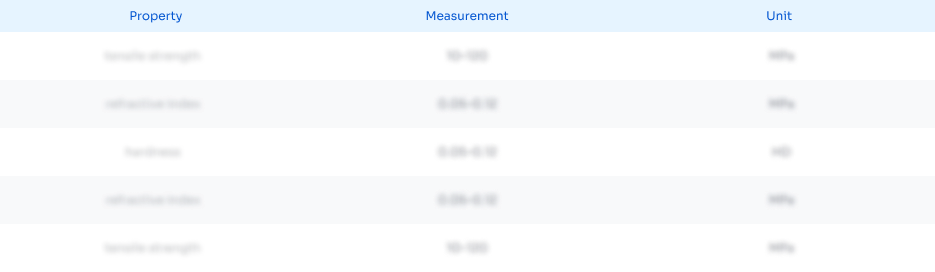
Abstract
Description
Claims
Application Information

- R&D Engineer
- R&D Manager
- IP Professional
- Industry Leading Data Capabilities
- Powerful AI technology
- Patent DNA Extraction
Browse by: Latest US Patents, China's latest patents, Technical Efficacy Thesaurus, Application Domain, Technology Topic, Popular Technical Reports.
© 2024 PatSnap. All rights reserved.Legal|Privacy policy|Modern Slavery Act Transparency Statement|Sitemap|About US| Contact US: help@patsnap.com