One-dimensional positioning method of motion platform based on linear magnetic steel array
A motion platform, magnetic steel array technology, applied in the direction of using electric/magnetic devices to transfer sensing components, etc., can solve the problems of measurement accuracy loss, high cost, complex circuits and optical equipment, etc.
- Summary
- Abstract
- Description
- Claims
- Application Information
AI Technical Summary
Problems solved by technology
Method used
Image
Examples
Embodiment
[0046] The minimum number of the linear Hall sensors 5 placed on the motion platform 4 is determined by the number of unknown parameters contained in the linear magnetic steel array 2 magnetic flux density distribution model, and on this basis, the more the number of placed The more, the more beneficial it is to reduce the uncertainty of the motion platform 4 phase solution results, therefore, n is at least equal to 2.
[0047] refer to image 3 In the following, two linear Hall sensors 5 (ie n=2) are placed on the moving direction of the surface of the moving platform 4, and the unscented Kalman filter algorithm is used as an example to describe the present invention, so as to further understand the present invention.
[0048] 1) Select any two different positions within one pole pitch of the linear magnetic steel array 2 on the surface movement direction of the motion platform 4 in the motion system, and place a linear Hall sensor 5 at each position;
[0049] 2) Determine t...
PUM
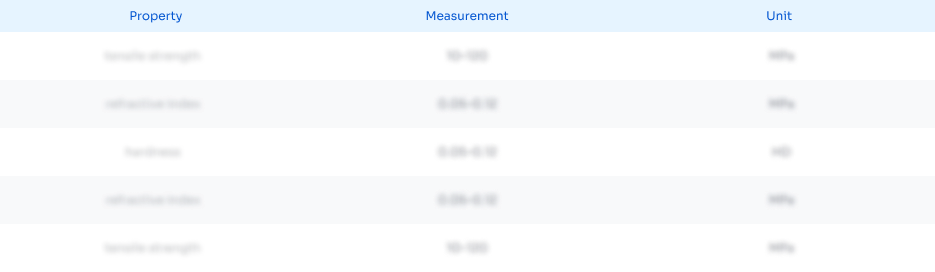
Abstract
Description
Claims
Application Information

- R&D Engineer
- R&D Manager
- IP Professional
- Industry Leading Data Capabilities
- Powerful AI technology
- Patent DNA Extraction
Browse by: Latest US Patents, China's latest patents, Technical Efficacy Thesaurus, Application Domain, Technology Topic, Popular Technical Reports.
© 2024 PatSnap. All rights reserved.Legal|Privacy policy|Modern Slavery Act Transparency Statement|Sitemap|About US| Contact US: help@patsnap.com