Glucose production process for reducing steam consumption
A production process and technology for glucose, applied in the field of glucose production technology, can solve the problems of waste of heat energy, large amount of steam used, etc., and achieve the effect of reducing production costs
- Summary
- Abstract
- Description
- Claims
- Application Information
AI Technical Summary
Problems solved by technology
Method used
Image
Examples
Embodiment Construction
[0010] Glucose production process, which includes decolorization, ion exchange, evaporation and other processes: add a plate heat exchanger before decolorization, through the heat exchanger, use 90 ℃ steam condensed water to heat the 35 ℃ glucose mother liquor to increase its temperature from 35 ℃ If the temperature is 65°C, reduce the amount of steam that needs to be heated to 85°C for decolorization. This part reduces the amount of steam by 1.75T / h.
[0011] After decolorization and before ion exchange, add a plate heat exchanger, heat the ion exchange output at 50 °C with the material at 85 °C after decolorization, and the ion exchange output after heating to 55 °C goes to the evaporator.
[0012] After ion exchange and before evaporation, a plate heat exchanger is added, and the evaporator output at 70°C is used to heat the ion exchange output at 55°C. After heating to 60°C, it enters the evaporator for evaporation operation. This process reduces the evaporator The steam c...
PUM
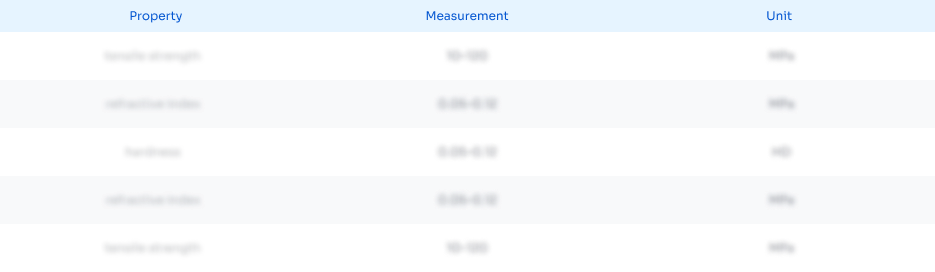
Abstract
Description
Claims
Application Information

- Generate Ideas
- Intellectual Property
- Life Sciences
- Materials
- Tech Scout
- Unparalleled Data Quality
- Higher Quality Content
- 60% Fewer Hallucinations
Browse by: Latest US Patents, China's latest patents, Technical Efficacy Thesaurus, Application Domain, Technology Topic, Popular Technical Reports.
© 2025 PatSnap. All rights reserved.Legal|Privacy policy|Modern Slavery Act Transparency Statement|Sitemap|About US| Contact US: help@patsnap.com