Method for preparing polycarbonate
A technology of polycarbonate and polyethylene glycol, applied in the field of polymer material preparation, to achieve the effect of reducing dosage, increasing utilization rate, and improving utilization rate
- Summary
- Abstract
- Description
- Claims
- Application Information
AI Technical Summary
Problems solved by technology
Method used
Image
Examples
Embodiment 1
[0033] The synthesis of embodiment 1 amphiphilic macromolecular catalyst
[0034] Taking polyethylene glycol-block-poly-4-vinylpyridine as an example, the synthesis of amphiphilic macromolecular catalysts is divided into the following four steps:
[0035] 1. Synthesis of Dithiobenzoic Acid
[0036] 1.1 Grignard reagent preparation
[0037] Bromobenzene (5.6g, 0.036mol) and magnesium sticks (0.82g, 0.036mol) were stirred in THF (100ml) to obtain Grignard reagent.
[0038] 1.2 Synthesis of dithiobenzoic acid
[0039] At -5°C, a THF solution (30ml) of carbon disulfide (2.7g, 0.036mol) was added to the above Grignard reagent solution, and reacted for 1h. Then 5 mL of water was added dropwise and stirring was continued for 30 min. Suction filtration, remove THF under reduced pressure. Add dilute hydrochloric acid to acidify (10%, v / v), CH 2 Cl 2extraction. The organic phase was extracted three times with cold NaOH solution (10%), acidified and extracted. repeat three times...
Embodiment 2
[0055] Dissolve 6.03g of bisphenol A, 2.2012g of sodium hydroxide, 48mg of sodium dithionite and 4mg of tert-butylphenol in 44mL of water to form an aqueous phase, stir, and the pH is 12.
[0056] 10 mg of polyethylene glycol-block-poly-4-vinylpyridine (wherein n is 10) prepared by the method described in Example 1 was dissolved in 2 mL of dichloromethane and added to the above system; then 1.263 g of triphosgene Dissolved in 12mL of dichloromethane. Add the dichloromethane solution of triphosgene into the system, stir, and react at 30°C for 30 minutes, and keep the pH value of the system at 10-10.5 during the reaction.
[0057] Upon completion of the phosgenation reaction, chloroformate was detected using 4-(4-nitrobenzyl)pyridine (NBP) as described by A.N. Agree et al. (talanta, 1996, vol. 13. p. 1151-1160). The measured chloroformate content was 4.89% (mass fraction). No phenol precipitates out after the wastewater phase is acidified after the reaction. The above procedu...
Embodiment 3
[0059] The steps of Example 2 were repeated, except that the amount of polyethylene glycol-block-poly-4-vinylpyridine added was 73.7 mg, and the content of chloroformate was determined to be 0.5% (mass fraction).
[0060] And when adding equimolar equivalent triethylamine 1.5mL as catalyst in the reaction mixture, it was found that the chloroformate in the product obtained could not be detected, indicating that the chloroformate in the polymer was completely hydrolyzed.
PUM
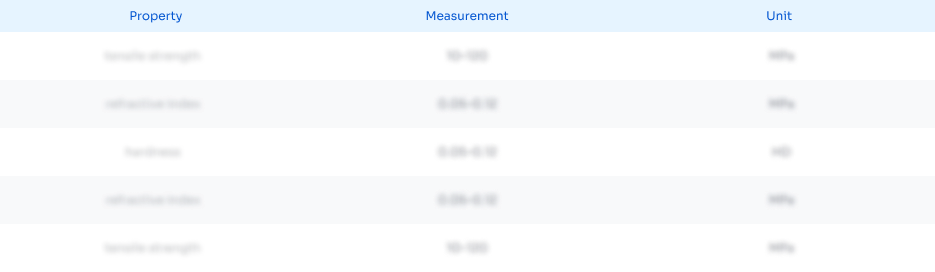
Abstract
Description
Claims
Application Information

- R&D
- Intellectual Property
- Life Sciences
- Materials
- Tech Scout
- Unparalleled Data Quality
- Higher Quality Content
- 60% Fewer Hallucinations
Browse by: Latest US Patents, China's latest patents, Technical Efficacy Thesaurus, Application Domain, Technology Topic, Popular Technical Reports.
© 2025 PatSnap. All rights reserved.Legal|Privacy policy|Modern Slavery Act Transparency Statement|Sitemap|About US| Contact US: help@patsnap.com