Producing process of wall and floor tile crack glaze
A production process and technology of cracked glaze, which is applied in the field of production process of cracked glaze for wall and floor tiles. It can solve the problems of inconsistency, unreal effect, and no strong concave-convex feel, etc., and achieve comfortable hand feeling, guaranteed strength, and smooth and delicate cracked surface. Effect
- Summary
- Abstract
- Description
- Claims
- Application Information
AI Technical Summary
Problems solved by technology
Method used
Image
Examples
Embodiment 1
[0030] The parameters of the glazing process are: bottom glaze moisture (%) is 40, specific gravity (g / ml) is 1.60, viscosity (Mpa.S) is 80, glaze amount (g) is 120; surface glaze moisture (%) is 44, specific gravity (g / ml) is 1.80, the viscosity (Mpa.S) is 600, and the glaze amount (g) is 150.
Embodiment 2
[0032] The glazing process parameters are: bottom glaze moisture (%) is 44, specific gravity (g / ml) is 1.75, viscosity (Mpa.S) is 100, glaze amount (g) is 100; surface glaze moisture (%) is 39, specific gravity (g / ml) is 1.66, viscosity (Mpa.S) is 520, glaze amount (g) is 80.
Embodiment 3
[0034] The parameters of the glazing process are: bottom glaze moisture (%) is 42, specific gravity (g / ml) is 1.71, viscosity (Mpa.S) is 400, glaze amount (g) is 200; surface glaze moisture (%) is 41, specific gravity (g / ml) is 1.70, viscosity (Mpa.S) is 400, glaze amount (g) is 100.
PUM
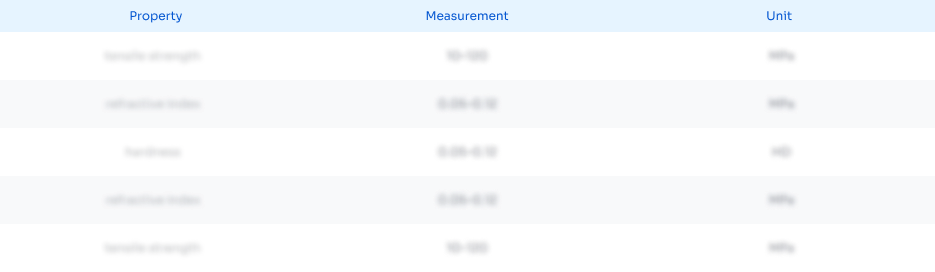
Abstract
Description
Claims
Application Information

- R&D
- Intellectual Property
- Life Sciences
- Materials
- Tech Scout
- Unparalleled Data Quality
- Higher Quality Content
- 60% Fewer Hallucinations
Browse by: Latest US Patents, China's latest patents, Technical Efficacy Thesaurus, Application Domain, Technology Topic, Popular Technical Reports.
© 2025 PatSnap. All rights reserved.Legal|Privacy policy|Modern Slavery Act Transparency Statement|Sitemap|About US| Contact US: help@patsnap.com