Exhaust valve seat for automobile engine
A technology for automobile engines and exhaust valves, applied to engine components, machines/engines, mechanical equipment, etc., can solve problems such as increased tool wear, increased scrap rate and cost, and reduced tool life, achieving production cost advantages and low cost Effect
- Summary
- Abstract
- Description
- Claims
- Application Information
AI Technical Summary
Problems solved by technology
Method used
Image
Examples
Embodiment 1
[0014] Embodiment 1: adopt the material of following chemical composition content to make engine exhaust valve seat: (weight percentage)
[0015] C: 1.08%, Mo: 6.58%, Cr: 3.5%, Co: 5.51%, Ni: 2.28%, V: 0.72%, Cu0.56%, and the rest Fe.
[0016] The production process is:
[0017] Ingredients → forming → sintering → machining → external inspection → packaging.
[0018] 250 times the metallographic structure of the exhaust valve seat made by figure 1 shown.
Embodiment 2
[0019] Example 2: C: 1.12%, Mo: 6.6%, Cr: 3.55%, Co: 5.54%, Ni: 2.31%, V: 0.7%, Cu0.55%, and the rest Fe.
[0020] The manufacturing process is the same as example 1.
[0021] The above-mentioned exhaust valve seat is suitable for high-performance supercharged engines with a displacement of 1.8L and above, and has the characteristics of low cost and high performance.
PUM
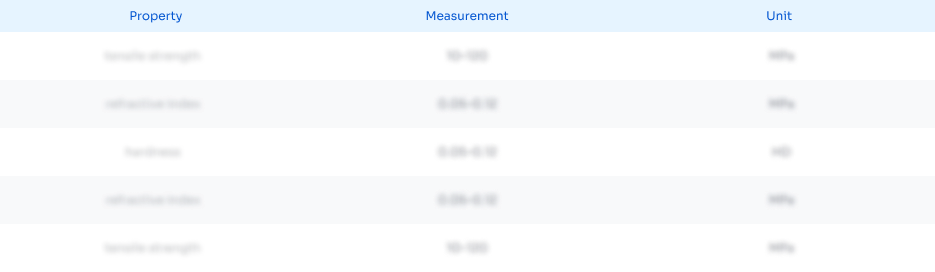
Abstract
Description
Claims
Application Information

- R&D Engineer
- R&D Manager
- IP Professional
- Industry Leading Data Capabilities
- Powerful AI technology
- Patent DNA Extraction
Browse by: Latest US Patents, China's latest patents, Technical Efficacy Thesaurus, Application Domain, Technology Topic, Popular Technical Reports.
© 2024 PatSnap. All rights reserved.Legal|Privacy policy|Modern Slavery Act Transparency Statement|Sitemap|About US| Contact US: help@patsnap.com