Method for assembling multi-link suspension
An assembly method and multi-link technology, applied in metal processing, metal processing equipment, manufacturing tools, etc., can solve problems such as inability to meet assembly requirements, long time cycle, and high labor intensity
- Summary
- Abstract
- Description
- Claims
- Application Information
AI Technical Summary
Problems solved by technology
Method used
Image
Examples
Embodiment Construction
[0023] Such as figure 1 As shown, this kind of multi-link suspension usually adopts hinge connection between the connecting parts, so it is generally connected offline first. figure 1 The shown front trailing arm 1, brake assembly 2, stabilizer bar 3, upper cross arm 4, subframe 5 and lower swing arm 6 are connected by bolts to form a total rear suspension assembly module, Then assemble the coil spring 7, the specific steps and operation methods are as follows:
[0024] As shown in Figure 1, among the parts of the rear suspension assembly, except for the coil spring 7, other parts can be assembled offline into an assembly module, and then hoisted to the fixture of the lifting trolley (AGV) (The lifting trolley and the production line spreader are accompanied by synchronously), use the lifting trolley to lift the rear suspension assembly to the joint assembly position with the vehicle body, and then tighten the connecting bolts of the sub-frame 5 and the front trailing arm 1 t...
PUM
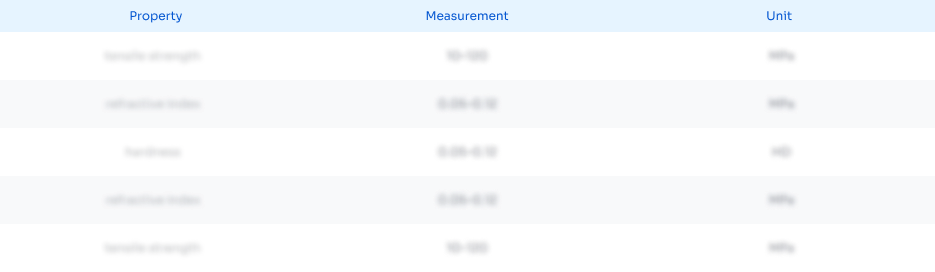
Abstract
Description
Claims
Application Information

- R&D
- Intellectual Property
- Life Sciences
- Materials
- Tech Scout
- Unparalleled Data Quality
- Higher Quality Content
- 60% Fewer Hallucinations
Browse by: Latest US Patents, China's latest patents, Technical Efficacy Thesaurus, Application Domain, Technology Topic, Popular Technical Reports.
© 2025 PatSnap. All rights reserved.Legal|Privacy policy|Modern Slavery Act Transparency Statement|Sitemap|About US| Contact US: help@patsnap.com