Magnetic suspension spherical active joint
A technology of active joints and magnetic levitation, applied in the directions of manipulators, manufacturing tools, joints, etc., can solve the problems of decreased precision, slow response and low efficiency of the control system, and achieve the effect of good dynamic performance, fast response speed and simple structure
- Summary
- Abstract
- Description
- Claims
- Application Information
AI Technical Summary
Problems solved by technology
Method used
Image
Examples
Embodiment Construction
[0017] Such as figure 1 As shown, the magnetic levitation spherical active joint is composed of a spherical joint body, a power amplifier, an inverter, a rectifier regulator, a driver, a sensor, a signal processing circuit, and a DSP digital controller.
[0018] Such as figure 2 , image 3 As shown, the spherical joint body structure is composed of a base 9 supporting the joint, a joint rotor 3, a joint stator 5, a rotating arm 2, and the like. The base 9 and the magnetically suspended (bearingless) spherical joint stator 5 are fixed as a whole by connecting screws 17. The inner shape of the joint stator 5 is an open spherical inner surface, and a groove 11 is formed on the spherical inner surface, and the groove connects the entire spherical inner surface. It is divided into tiny unit faces with the same geometric shape to form an inner spherical salient pole stator. And along the grooves parallel to each three-dimensional coordinate plane with the center of the sphere as...
PUM
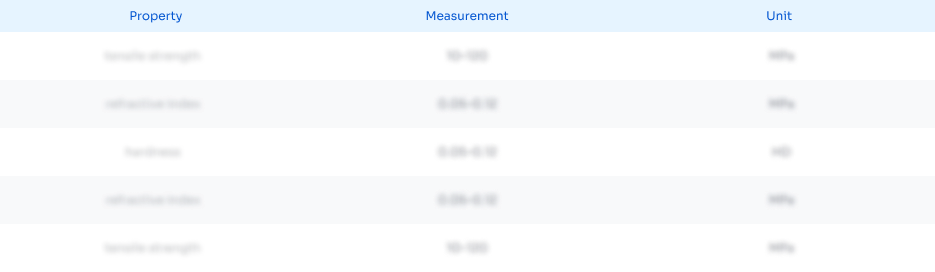
Abstract
Description
Claims
Application Information

- R&D
- Intellectual Property
- Life Sciences
- Materials
- Tech Scout
- Unparalleled Data Quality
- Higher Quality Content
- 60% Fewer Hallucinations
Browse by: Latest US Patents, China's latest patents, Technical Efficacy Thesaurus, Application Domain, Technology Topic, Popular Technical Reports.
© 2025 PatSnap. All rights reserved.Legal|Privacy policy|Modern Slavery Act Transparency Statement|Sitemap|About US| Contact US: help@patsnap.com