Spiral extrusion method and device for bar-producing machine
A technology of screw extrusion and rod making machine, which is applied in the direction of presses, manufacturing tools, and material forming presses, etc., which can solve the problems of short combustion time, poor gas discharge, and influence on temperature, so as to save equipment use costs, The effect of long burning time and fast temperature dissipation
- Summary
- Abstract
- Description
- Claims
- Application Information
AI Technical Summary
Problems solved by technology
Method used
Image
Examples
Embodiment Construction
[0021] The screw extrusion method and device of a rod making machine of the present invention will be further described in detail below in conjunction with the accompanying drawings and embodiments, but it is not used as a basis for any limitation of the present invention.
[0022] Example. The screw extrusion method of a kind of rod making machine of the present invention, as figure 1 shown. The method is to arrange the exhaust cylinder 3, the exhaust sleeve 4 and the compression sleeve 5 between the screw 1 and the inner sleeve 6, so that the material is pre-extruded to the compression sleeve 5 through the screw 1, the exhaust sleeve 3 and the exhaust sleeve 4. Inside, the material is extruded twice in the compression sleeve 5 and then output through the inner sleeve 6. A pusher 2 is provided at the rear end of the screw 1 to increase the feeding capacity of the rod making machine. Exhaust cylinder 3 is provided with main exhaust groove 14, and exhaust sleeve 4 is provide...
PUM
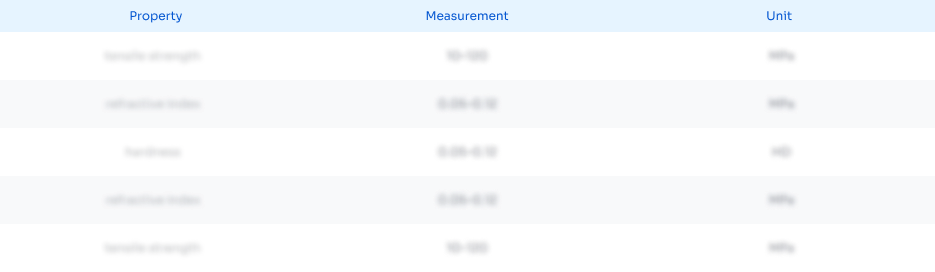
Abstract
Description
Claims
Application Information

- Generate Ideas
- Intellectual Property
- Life Sciences
- Materials
- Tech Scout
- Unparalleled Data Quality
- Higher Quality Content
- 60% Fewer Hallucinations
Browse by: Latest US Patents, China's latest patents, Technical Efficacy Thesaurus, Application Domain, Technology Topic, Popular Technical Reports.
© 2025 PatSnap. All rights reserved.Legal|Privacy policy|Modern Slavery Act Transparency Statement|Sitemap|About US| Contact US: help@patsnap.com