Acquisition method of three freedom-degree transportation industrial robot multiple-objective optimization design parameter
An industrial robot and multi-objective optimization technology, which is applied in the field of acquisition of multi-objective optimization design parameters of three-degree-of-freedom handling industrial robots, can solve problems such as inability to take into account design indicators and affect the overall performance of the system
- Summary
- Abstract
- Description
- Claims
- Application Information
AI Technical Summary
Problems solved by technology
Method used
Image
Examples
Embodiment 1
[0231] 1. A method for obtaining multi-objective optimization design parameters of a three-degree-of-freedom handling industrial robot, the three-degree-of-freedom handling industrial robot comprising: a first mechanical arm (1), a second mechanical arm (2), and a third mechanical arm (3) The two ends of the second manipulator (2) are respectively connected to one end of the first manipulator (1) and one end of the third manipulator (3), which is characterized in that the method for obtaining multi-objective optimization design parameters includes The following steps:
[0232] Step 1 First, establish the linkage coordinate system of the three-degree-of-freedom manipulator, such as figure 1 As shown; from the kinematic equation of the robotic arm, the trajectory of the end working point can be obtained as x 2 + y 2 + ( z - ...
Embodiment 2
[0415] The basic design requirements for the three-degree-of-freedom handling robot are: the working space of the three-degree-of-freedom industrial robot is centered at (0, 0, 1), and the maximum radius is R max =1.5, the minimum radius R min = 0.2 The part between the two balls (unit: m). The maximum load mass required to be handled is 25kg. On this basis, the work space is required to be maximized, the strength meets the material requirements, and the energy and time performance of the robotic arm control process are optimal.
[0416] For the three-degree-of-freedom handling robot in this design, through the analysis in Chapter 3, 12 parameters that characterize the mechanical design parameters and reflect the motor performance parameters are determined as the design variables of the entire design process. At the same time, for the mechanical parameters of the robotic arm 1 1 , R 1 , R 1 , And the inner cavity parameter h of the robot arms 2 and 3 2e , B 2e , H 3e , B 3e Becaus...
PUM
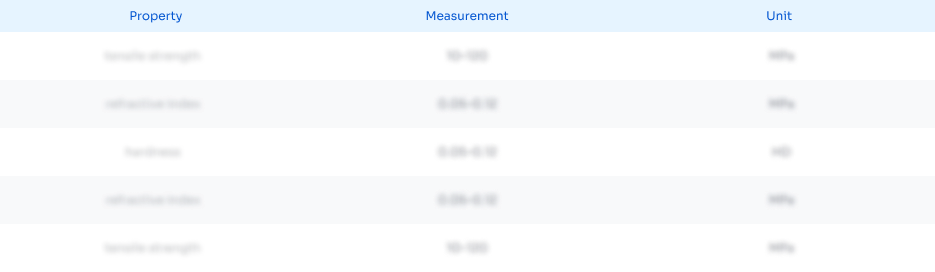
Abstract
Description
Claims
Application Information

- R&D
- Intellectual Property
- Life Sciences
- Materials
- Tech Scout
- Unparalleled Data Quality
- Higher Quality Content
- 60% Fewer Hallucinations
Browse by: Latest US Patents, China's latest patents, Technical Efficacy Thesaurus, Application Domain, Technology Topic, Popular Technical Reports.
© 2025 PatSnap. All rights reserved.Legal|Privacy policy|Modern Slavery Act Transparency Statement|Sitemap|About US| Contact US: help@patsnap.com