Body propelling integrated outer appearance modeling process for supersonic aircraft
A technology of hypersonic speed and modeling method, which is applied in 3D modeling, instrumentation, image data processing, etc., can solve the problems of inconvenient adoption, complex geometric shape of the aircraft, and no systematic solution for the parameterization of the geometric shape of the aircraft. Simplicity of the modeling process
- Summary
- Abstract
- Description
- Claims
- Application Information
AI Technical Summary
Problems solved by technology
Method used
Image
Examples
Embodiment Construction
[0046] The present invention will be further described in detail below in conjunction with the accompanying drawings.
[0047] The design flow chart of its modeling method is as follows: figure 1 As shown, the specific steps are as follows:
[0048] (1) Design the geometric profile of the two-dimensional flow channel of the propulsion system
[0049] Under the constraint of the total length of the aircraft, the design of the flow channel of the propulsion system of the hypersonic aircraft, including the precursor inlet ( figure 2 1 in), combustion chamber ( figure 2 2 in), rear body nozzle ( figure 2 3) in three parts. The precursor inlet is composed of multiple compression wedges; the combustion chamber is composed of equal-section isolation sections ( figure 2 4) and expansion segment ( figure 25) in the composition; the rear body nozzle is in the form of a curve. The flow channel of the entire propulsion system forms the lower surface of the hypersonic vehicle, ...
PUM
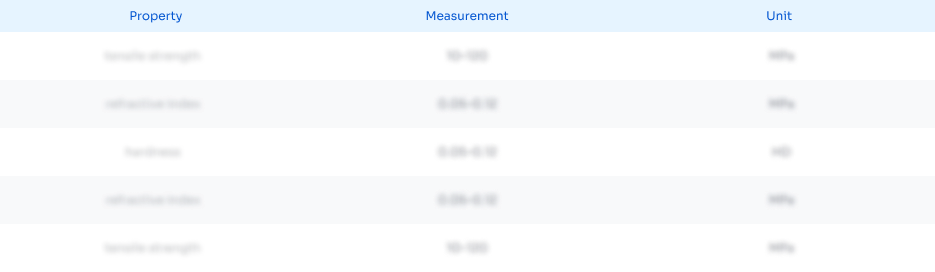
Abstract
Description
Claims
Application Information

- Generate Ideas
- Intellectual Property
- Life Sciences
- Materials
- Tech Scout
- Unparalleled Data Quality
- Higher Quality Content
- 60% Fewer Hallucinations
Browse by: Latest US Patents, China's latest patents, Technical Efficacy Thesaurus, Application Domain, Technology Topic, Popular Technical Reports.
© 2025 PatSnap. All rights reserved.Legal|Privacy policy|Modern Slavery Act Transparency Statement|Sitemap|About US| Contact US: help@patsnap.com