System and method for part process feature detection in three-coordinate numerical control machining
A technology of parts processing and feature detection, applied in the direction of digital control, electrical program control, etc., can solve problems such as not considering process resources, failing to give correct detection results, and having no practical processing meaning
- Summary
- Abstract
- Description
- Claims
- Application Information
AI Technical Summary
Problems solved by technology
Method used
Image
Examples
Embodiment Construction
[0093] The embodiments of the present invention are described in detail below in conjunction with the accompanying drawings: this embodiment is implemented on the premise of the technical solution of the present invention, and detailed implementation methods and specific operating procedures are provided, but the protection scope of the present invention is not limited to the following the described embodiment.
[0094] Such as figure 1 As shown, it is a structural block diagram of the system of the present invention for component processing feature detection in three-coordinate numerical control machining, including: feature detection system integration platform 1, tool information update module 2, part information input module 3, processing surface determination module 4, Surface processing method generation method update module 5, surface processing method generation module 6, surface processing method feasibility detection module 7, feature factor extraction module 8, feat...
PUM
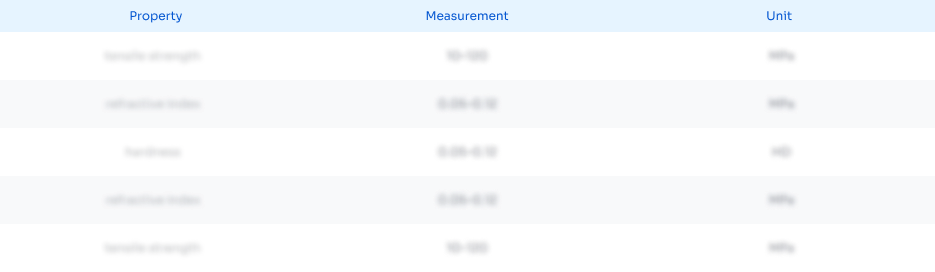
Abstract
Description
Claims
Application Information

- Generate Ideas
- Intellectual Property
- Life Sciences
- Materials
- Tech Scout
- Unparalleled Data Quality
- Higher Quality Content
- 60% Fewer Hallucinations
Browse by: Latest US Patents, China's latest patents, Technical Efficacy Thesaurus, Application Domain, Technology Topic, Popular Technical Reports.
© 2025 PatSnap. All rights reserved.Legal|Privacy policy|Modern Slavery Act Transparency Statement|Sitemap|About US| Contact US: help@patsnap.com