Seamless connection method for off-line programming and on-site debugging of robot
An off-line programming and on-site debugging technology, which is applied in the direction of manipulators, program-controlled manipulators, manufacturing tools, etc., can solve problems such as seamless connection, occupation of robot working time, damage to fixtures or robots, etc., to improve the use effect and improve processing and manufacturing and installation accuracy, the effect of eliminating deviation
- Summary
- Abstract
- Description
- Claims
- Application Information
AI Technical Summary
Problems solved by technology
Method used
Examples
Embodiment 1
[0043] A method for seamless connection between off-line programming and on-site debugging of a robot, the steps are as follows:
[0044] a. Design the 3D models of the fixtures and robot tools, and import the 3D models of the fixtures and robot tools and the robot model (provided by the robot manufacturer) into the robot offline programming software;
[0045] b. In the off-line programming software of the robot, conduct a preliminary inspection of the process feasibility of the fixture, robot tool and robot. If existing design problems and potential risks are found, it is necessary to redesign the 3D of the fixture and robot tool in a targeted manner Model or re-select the model of the robot, repeat steps a and b until the process feasibility of the fixture, robot tool and robot is all right;
[0046] c. Install the fixtures, robots and robot tools in the field environment in place according to the installation positions of the fixtures, robots and robot tools in the ...
Embodiment 2
[0052] The specific method for making the installation of the robot tool in the off-line programming software of the robot consistent with the actual installation in the field environment described in step d in embodiment 1 is:
[0053] 1) Create a new empty trajectory program in the real robot system;
[0054] 2) Switch the robot to the tool0 tool coordinate system movement mode, move the robot to a place with a looser space and record a POS_A point;
[0055] 3) Lock the X and Z axes of the robot tool0 tool coordinate system through the direction lock key, move the robot forward for a certain distance to the Y axis, and record a POS_B point;
[0056] 4), move the robot back to POS_A point;
[0057] 5) Lock the Y and Z axes of the robot tool0 tool coordinate system through the direction lock key, move the robot to the positive direction of the X axis for a certain distance, and record a POS_C point;
[0058] 6) Use a mobile three-coordinate measuring instrument...
Embodiment approach
[0064] On the basis of embodiment 1 or 2, in step e in embodiment 1, the specific method for measuring the relative position of the tooling fixture coordinate system actually installed in place in the field environment in the robot base coordinate system is as follows:
[0065] A. Use a mobile three-coordinate measuring instrument to first find out the coordinate system of the fixture;
[0066] B. Create a new empty trajectory program in the real robot system;
[0067] C. Move the robot tool near or above the fixture, use the robot base coordinate system to record the position of the tip point of the robot tool in the trajectory program, read the coordinate value of the tip point of the robot tool in the robot base coordinate system, and fill in Enter the corresponding position in the coordinate system conversion software; use the mobile three-coordinate measuring instrument to measure the coordinate value of the tip point of the robot tool in the fixture coordinate sy...
PUM
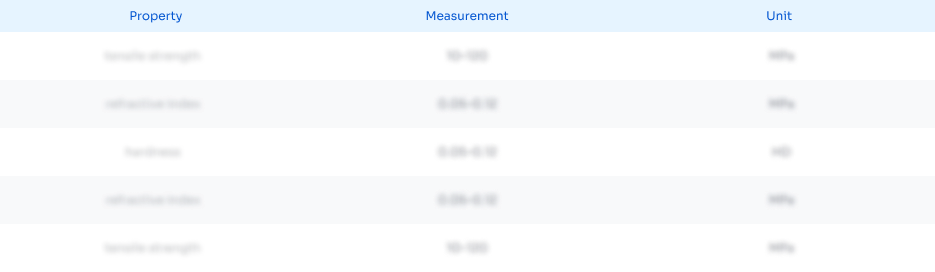
Abstract
Description
Claims
Application Information

- Generate Ideas
- Intellectual Property
- Life Sciences
- Materials
- Tech Scout
- Unparalleled Data Quality
- Higher Quality Content
- 60% Fewer Hallucinations
Browse by: Latest US Patents, China's latest patents, Technical Efficacy Thesaurus, Application Domain, Technology Topic, Popular Technical Reports.
© 2025 PatSnap. All rights reserved.Legal|Privacy policy|Modern Slavery Act Transparency Statement|Sitemap|About US| Contact US: help@patsnap.com