Plastic rubber model manufacturing method and product thereof
A production method and model technology, which is applied in the field of plastic technology and products, can solve the problems that two separate parts cannot be closely matched, the appearance of the plastic model is not beautiful, and the effect of viewing is affected, so as to facilitate large-scale promotion and application, and is easy to form a scale The effect of modernized production and simple process
- Summary
- Abstract
- Description
- Claims
- Application Information
AI Technical Summary
Problems solved by technology
Method used
Image
Examples
Embodiment 1
[0030] Embodiment 1: refer to figure 1 , a production method of plastic model, it comprises the following steps:
[0031] (1) Mixing equipment is set: mixing kettle 11, water removal kettle 22, coloring kettle 44, coloring kettle 55 and coloring kettle 66 are set at different positions successively, and water removal kettle 22 is combined with mixing kettle 11 and three The coloring kettles are connected through pipelines, and the water removal kettle 22 and several coloring kettles are also connected with the vacuum pump 33 through pipelines, valve 1, valve 2, valve 3, valve 4, valve 5, valve 6, valve 8 , valve 9, valve 41, valve 51 and valve 61 are respectively arranged on each connecting pipeline, and when the device is not activated, each valve is in a closed state, and the lower end of each coloring kettle is provided with a discharge port;
[0032] (2) Weighing: take raw materials according to the formula shown in the second column of Table 1;
[0033] (3) Mixing: put ...
Embodiment 2
[0044]Embodiment 2: The production method of the plastic model provided by this embodiment and the products thereof are basically the same as in Embodiment 1, the difference being that in step (2), the ratio of each raw material is as shown in the third column of Table 1, In step (9), the weight ratio of potassium nitrate to sodium nitrite is 1:1.
Embodiment 3
[0045] Embodiment 3: The production method of the plastic model provided by this embodiment and its products are basically the same as in Embodiment 1, except that in step (2), the ratio of each raw material is as shown in the fourth column of Table 1, In step (9), the weight ratio of potassium nitrate to sodium nitrite is 1:1.2.
[0046] The present invention is not limited to the above-mentioned embodiment, according to needs, can also be provided with coloring kettles loaded with other color pastes in sequence, and the setting of its valves and pipelines is similar to the setting of other several coloring kettles; if it is necessary to prepare thicker For the model, steps (10) and (11) can be repeated many times until the required thickness is reached; plastic products with different softness and hardness can be prepared by adjusting the ratio of each formula raw material; according to actual needs, multiple products can also be prepared. The plastic simulation model of a k...
PUM
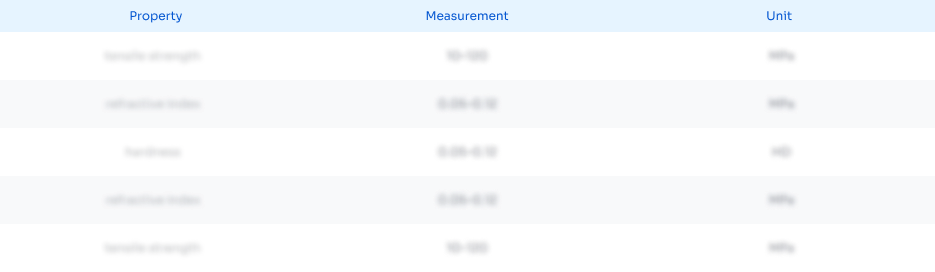
Abstract
Description
Claims
Application Information

- R&D
- Intellectual Property
- Life Sciences
- Materials
- Tech Scout
- Unparalleled Data Quality
- Higher Quality Content
- 60% Fewer Hallucinations
Browse by: Latest US Patents, China's latest patents, Technical Efficacy Thesaurus, Application Domain, Technology Topic, Popular Technical Reports.
© 2025 PatSnap. All rights reserved.Legal|Privacy policy|Modern Slavery Act Transparency Statement|Sitemap|About US| Contact US: help@patsnap.com