Phase changing method and apparatus of 3 phase salient brushless DC motor
A DC motor and DC current technology, applied in the direction of electronic commutator, etc., can solve the problems of poor reliability of rotor pre-positioning, uncertain initial position, complicated circuit debugging, etc., and achieve the elimination of positioning dead zone, high reliability, and detection method reliable effect
- Summary
- Abstract
- Description
- Claims
- Application Information
AI Technical Summary
Problems solved by technology
Method used
Image
Examples
Embodiment Construction
[0042] Such as figure 1 Shown is the flow chart of the commutation method of the present invention. First, direct current is applied to two of the three-phase windings of the three-phase salient-pole brushless DC motor, so that the stator winding generates a positioning magnetic potential, and the rotor is dragged into a certain position. Predicted initial position. Then, according to the initial position of the rotor and the target rotation direction, power is applied to the two-phase winding corresponding to the magnetic potential 120° ahead of the initial position of the rotor, and the initial value I1 of the energized current at this time is recorded. Then detect the change of the current value I2 of the stator two-phase winding that is currently powered on. When the current value I2 in the winding is equal to the initial value I1 of the current, the stator winding is commutated. At this time, the electric angle is 120° ahead of the current position of the rotor Accordin...
PUM
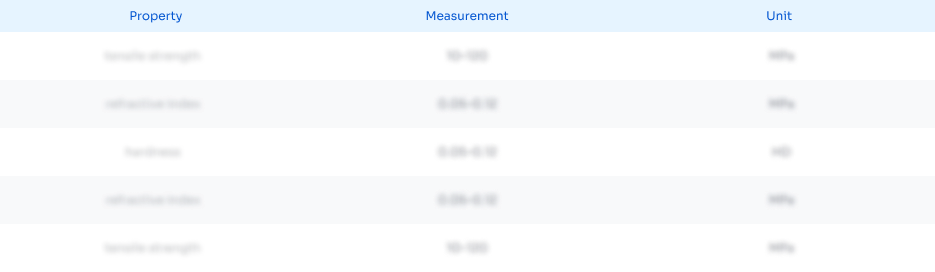
Abstract
Description
Claims
Application Information

- R&D
- Intellectual Property
- Life Sciences
- Materials
- Tech Scout
- Unparalleled Data Quality
- Higher Quality Content
- 60% Fewer Hallucinations
Browse by: Latest US Patents, China's latest patents, Technical Efficacy Thesaurus, Application Domain, Technology Topic, Popular Technical Reports.
© 2025 PatSnap. All rights reserved.Legal|Privacy policy|Modern Slavery Act Transparency Statement|Sitemap|About US| Contact US: help@patsnap.com