Three-axis accurate angular motion control method
A control method and technology of angular motion, applied in the direction of electric controller, adaptive control, general control system, etc., can solve the problem that the motion axis cannot be commanded to track accurately, the closed loop cannot work reliably, and the performance of the linkage angular rate is degraded. The effect of eliminating coupling torque disturbance between shafts, improving linkage performance and improving reliability
- Summary
- Abstract
- Description
- Claims
- Application Information
AI Technical Summary
Problems solved by technology
Method used
Image
Examples
Embodiment Construction
[0023] In each control servo cycle, the control calculation device generates the relative rotation angle mθ according to the harmonic characteristics of the inter-axis coupling torque disturbance. r ±nθ p Changing quadrature harmonic compensation control signal, and at the same time calculate and adjust the amplitude p of each order harmonic signal in real time according to the system servo error sl ,p cl , and the compensation control signal is applied to the basic closed-loop servo control loop independent of the corresponding axis, so as to achieve the purpose of accurately eliminating the coupling torque disturbance between the axes. By setting the initial phase shift angle β of the control signal sl , β cl , to compensate the system delay and ensure the stability of the adaptive mechanism.
[0024] The calculation formula of inter-shaft coupling torque harmonic adaptive feed-forward compensation (CTHAFC) is:
[0025] u CTHAFC ...
PUM
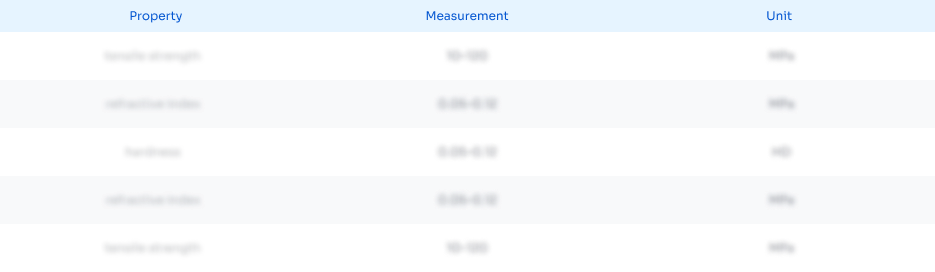
Abstract
Description
Claims
Application Information

- R&D
- Intellectual Property
- Life Sciences
- Materials
- Tech Scout
- Unparalleled Data Quality
- Higher Quality Content
- 60% Fewer Hallucinations
Browse by: Latest US Patents, China's latest patents, Technical Efficacy Thesaurus, Application Domain, Technology Topic, Popular Technical Reports.
© 2025 PatSnap. All rights reserved.Legal|Privacy policy|Modern Slavery Act Transparency Statement|Sitemap|About US| Contact US: help@patsnap.com