Roller screening pulp kneader
A pulper and drum technology, applied in the field of papermaking machinery, can solve the problems of wasting energy and reducing pulping efficiency, etc.
- Summary
- Abstract
- Description
- Claims
- Application Information
AI Technical Summary
Problems solved by technology
Method used
Image
Examples
Embodiment 1
[0021] Embodiment 1: As shown in Fig. 1 and Fig. 2, the drum screening pulper includes a pulper drum, and the pulper drum is divided into a pulping zone drum 11 and a screening zone drum 61, 62. The inner wall of the zone drum 11 is provided with a partition 2, and the structural form of the pulper drum is sequentially the first screening zone drum 61, the pulping zone drum 11 fixedly connected with the first screening zone drum 61, and the The drum 62 in the second screening area is fixedly connected to the drum 11 in the pulping area.
[0022] Spiral material guide plates 7 are fixed on the inner walls of the screening area drums 61 and 62 . The diameter of the screen drums 61 , 62 is smaller than the diameter of the pulping drum 11 . This structural form can make the drum 1 in the pulping area and the drum 6 in the screening area run at different rotational linear speeds, so as to ensure good decomposing and screening effects respectively.
[0023] The cross-sectional str...
Embodiment 2
[0025] Embodiment 2: As shown in Figure 4, this embodiment is basically the same as Embodiment 1, the difference is that the cylinder wall of the drum in the pulping area is also provided with screen holes, so that the drum in the pulping area has a screening function at the same time .
Embodiment 3
[0026] Embodiment 3: As shown in Figure 5, this embodiment is basically the same as Embodiment 1, the difference is that a pulp mixing drum 4 is provided at the entrance of the drum in the first screening area, and the function of this drum is to mix raw materials and water Thorough mixing is beneficial to the screening of raw materials by the drum 61 in the first screening zone. The structure of the pulp mixing drum 4 adopts the structure of the drum 41 as shown in FIG. 6 .
PUM
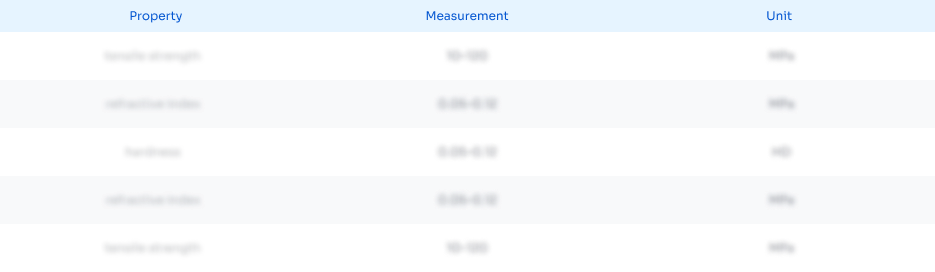
Abstract
Description
Claims
Application Information

- R&D Engineer
- R&D Manager
- IP Professional
- Industry Leading Data Capabilities
- Powerful AI technology
- Patent DNA Extraction
Browse by: Latest US Patents, China's latest patents, Technical Efficacy Thesaurus, Application Domain, Technology Topic, Popular Technical Reports.
© 2024 PatSnap. All rights reserved.Legal|Privacy policy|Modern Slavery Act Transparency Statement|Sitemap|About US| Contact US: help@patsnap.com