Assembly and method for mounting a pump bearing in/on plastic coolant pump housings
A technology for coolant pumps and pump bearings, which is applied to components of pumping devices for elastic fluids, rigid supports for bearing components, bearings, etc., which can solve problems such as increased processing costs, breakage, and weakened bearing necks, and achieve small Processing and assembly costs, improved service life, and less noise
- Summary
- Abstract
- Description
- Claims
- Application Information
AI Technical Summary
Problems solved by technology
Method used
Image
Examples
Embodiment Construction
[0046] exist figure 1 A possible design of the structure according to the invention is shown in a side view, a sectional view. figure 2 show according to figure 1 The dependent cross-sectional view X-X.
[0047] Here, a bearing ring 2 of a pump bearing 3 with at least one bearing groove 1 is arranged in a bearing seat 4 of a plastic coolant pump housing 5 . The bearing seat 4 is composed of many positioning short arms 7 combined with axial bearing shoulders 6 .
[0048] Between the positioning short arm 7 and the bearing shoulder 6, there are separate, i.e. independent, adhesive grooves 8, which are respectively equipped with liquid-tight walls 9 in four axial directions, that is, they have no connecting channels between them. .
[0049] Only above this adhesive groove 8, ie at the bearing ring 2 of the pump bearing 3 arranged there, also at the outer edge of the pump bearing 3, at the slot-shaped points of the adhesive pocket 10, is the adhesive. The contact tank is "op...
PUM
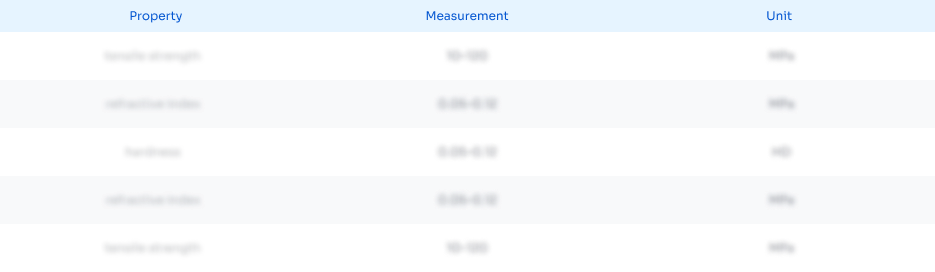
Abstract
Description
Claims
Application Information

- R&D Engineer
- R&D Manager
- IP Professional
- Industry Leading Data Capabilities
- Powerful AI technology
- Patent DNA Extraction
Browse by: Latest US Patents, China's latest patents, Technical Efficacy Thesaurus, Application Domain, Technology Topic, Popular Technical Reports.
© 2024 PatSnap. All rights reserved.Legal|Privacy policy|Modern Slavery Act Transparency Statement|Sitemap|About US| Contact US: help@patsnap.com