Hoist-transportating machine rail span, linearity automated detection method
A technology for lifting and transporting machinery and automatic detection, which is applied in the direction of transportation and packaging, measuring devices, instruments, etc., can solve the problems of hidden dangers in measurement safety operations and scattered workers, so as to reduce the number of measuring workers, eliminate hidden dangers of safety accidents, shorten Measuring the effect of working hours
- Summary
- Abstract
- Description
- Claims
- Application Information
AI Technical Summary
Problems solved by technology
Method used
Image
Examples
specific Embodiment approach
[0032] An automatic detection method for the span and straightness of a hoisting and transporting machinery track, which includes straightness measurement and span measurement, and includes the following steps,
[0033] Step 1, set a prism between the tracks as a common reference point;
[0034] Step 2, set up a total station on the head end C of a track A, and set up a measuring point prism that can move along the track on the track;
[0035] Step 3, make the measuring point prism move along the track from the head end C to the tail end E, and the total station measures and records the three-dimensional coordinates (x a 、y a ,z a ); at the same time refer to the height difference h between the record point of the public reference point and the total station c ;Height difference h and three-dimensional coordinates are determined in no particular order;
[0036] Step 4: Set up the total station and the measuring point prism at the head end D of another track B, so that the ...
PUM
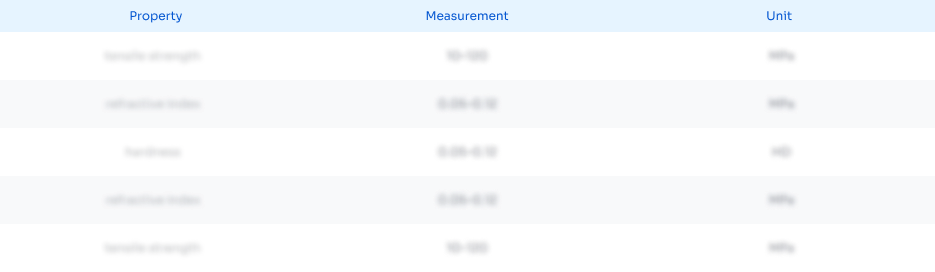
Abstract
Description
Claims
Application Information

- R&D
- Intellectual Property
- Life Sciences
- Materials
- Tech Scout
- Unparalleled Data Quality
- Higher Quality Content
- 60% Fewer Hallucinations
Browse by: Latest US Patents, China's latest patents, Technical Efficacy Thesaurus, Application Domain, Technology Topic, Popular Technical Reports.
© 2025 PatSnap. All rights reserved.Legal|Privacy policy|Modern Slavery Act Transparency Statement|Sitemap|About US| Contact US: help@patsnap.com