Method for manufacturing X100 pipeline steel submerged arc straight weld pipe
A technology of straight seam submerged arc and manufacturing methods, applied in the direction of manufacturing tools, arc welding equipment, welding media, etc., to achieve the effects of reducing heat input, improving performance, and easy processing
- Summary
- Abstract
- Description
- Claims
- Application Information
AI Technical Summary
Problems solved by technology
Method used
Examples
Embodiment 1
[0024] The manufacturing method of the present embodiment comprises the following steps:
[0025] 1. The chemical composition is C 0.06%, Si 0.30%, Mn 2.0%, P≤0.005, S≤0.0003, V+Nb+Ti 0.06%, Ni+Cr+Cu 0.6%, Cr+Mo+Mn 2% 14.3mm thick X100 controlled rolling steel plate.
[0026] 2. For edge milling, the bevel size is , the angle is 40°, the blunt edge is 4mm, and the bevel depth is 6mm.
[0027] 3. Pre-bend the edge, use the pre-bending machine to pre-bend the edge of the plate, so that the curvature of the edge of the plate meets the requirements.
[0028] 4. JCO forming. On the JCO forming machine, one side of the steel plate after pre-bending is firstly stamped 9 times, and the steel plate on this side is pressed into a semicircle, that is, the entire steel plate becomes a J shape, and then the other side of the steel plate is pressed into a semicircle. Half of it is bent by the same method and pass, and the steel plate is C-shaped at this time, and then the middle part of t...
Embodiment 2
[0049] The difference between this embodiment and embodiment 1 is:
[0050] The stamping frequency in step 4 adopts 21 stampings, that is, half of the steel plate is stamped 10 times respectively, and then a stamping is performed in the middle of the steel plate to make the steel plate into an open O-shaped;
[0051] The four-wire submerged arc automatic welding process in step 6 is: the current of the first wire is 800A, and the voltage is 32V; the current of the second wire is 650A, and the voltage is 36V; the current of the third wire is 500A, and the voltage is 38V; The current is 450A, the voltage is 40V; the welding wire spacing is 18mm, and the welding speed is 170mm / min.
[0052] The four-wire submerged arc automatic welding process in step 7 is as follows: the current of the first wire is 900A, and the voltage is 32V; the current of the second wire is 700A, and the voltage is 36V; the current of the third wire is 500A, and the voltage is 40V; The current is 450A, the...
PUM
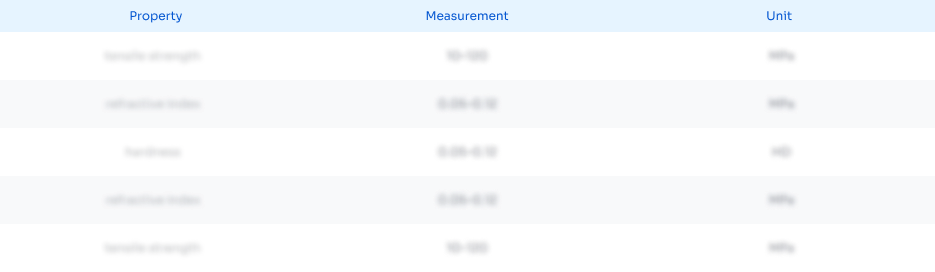
Abstract
Description
Claims
Application Information

- Generate Ideas
- Intellectual Property
- Life Sciences
- Materials
- Tech Scout
- Unparalleled Data Quality
- Higher Quality Content
- 60% Fewer Hallucinations
Browse by: Latest US Patents, China's latest patents, Technical Efficacy Thesaurus, Application Domain, Technology Topic, Popular Technical Reports.
© 2025 PatSnap. All rights reserved.Legal|Privacy policy|Modern Slavery Act Transparency Statement|Sitemap|About US| Contact US: help@patsnap.com