Marine cylinder oil and method for processing same
A cylinder oil and marine technology, applied in the field of lubricating oil, can solve the problems of cylinder liner and piston surface corrosion, inability to neutralize acidic substances, etc.
- Summary
- Abstract
- Description
- Claims
- Application Information
AI Technical Summary
Problems solved by technology
Method used
Image
Examples
Embodiment Construction
[0010] The present invention is made by mixing base oils of 400SN and 150BS, calcium sulfide alkyl phenolate, calcium naphthenate, calcium sulfonate with high base value, ashless dispersant, and antioxidant. The proportion of each component is: 400SN44 Parts, 11 parts of 150BS, 20 parts of calcium sulfide alkylphenate, 13 parts of calcium naphthenate, 7 parts of high base value calcium sulfonate, 4 parts of ashless dispersant, 1 part of antioxidant, its performance parameters: kinematic viscosity 16.3- 2 / s, pour point≤-5℃, flash point≥210℃, total base value≥98mgKOH / g, viscosity index≥70, moisture content≤0.06%, copper corrosion (100℃, 3h)≤1 level.
[0011] The process of the present invention is described below in conjunction with the accompanying drawings: the correctly measured base oil of 400SN and 150BS is fed into the blending kettle and heated to 70±5°C, and the best temperature is 70°C. If the oil contains water, it is heated to 100°C for dehydration, and it is circulated ...
PUM
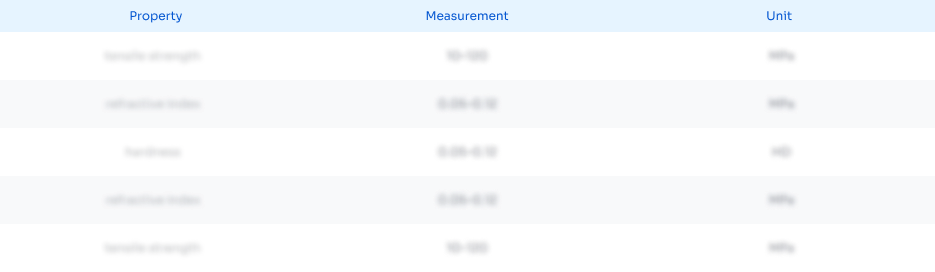
Abstract
Description
Claims
Application Information

- R&D
- Intellectual Property
- Life Sciences
- Materials
- Tech Scout
- Unparalleled Data Quality
- Higher Quality Content
- 60% Fewer Hallucinations
Browse by: Latest US Patents, China's latest patents, Technical Efficacy Thesaurus, Application Domain, Technology Topic, Popular Technical Reports.
© 2025 PatSnap. All rights reserved.Legal|Privacy policy|Modern Slavery Act Transparency Statement|Sitemap|About US| Contact US: help@patsnap.com