Method for measuring intaglio print ink printing plate ink-consumption amount
A technique of gravure printing ink and measurement method, which is applied to general parts of printing machinery, printing, printing machines, etc., can solve difficult problems such as ink volume, and achieve the effect of simple operation and accurate measurement results
- Summary
- Abstract
- Description
- Claims
- Application Information
AI Technical Summary
Problems solved by technology
Method used
Examples
Embodiment 1
[0016] In the state of normal process printing of gravure printing machine, about 250ml of plate wiping stock solution and waste liquid are randomly extracted from the plate wiping stock solution storage tank corresponding to the machine and the waste water outlet next to the machine respectively. In the laboratory in advance, place the evaporating dish in an oven at 105°C for 3 hours to keep the weight constant and record the weight. After mixing the extracted solution evenly, immediately use a 50ml pipette to extract three identical wiper stock solutions and waste solutions, respectively, and fill them in evaporating dishes with constant weight, then place them on a water bath, and evaporate to dryness. Finally, place the evaporating dish in an oven at 105°C to dry for 6 hours to constant weight, then cool for 30 minutes, weigh and record. The weight of the waste liquid after evaporating to a constant weight is recorded as: W1; the weight of the wiping stock solution after e...
Embodiment 2
[0020] In the state of normal process printing of gravure printing machine, about 250ml of plate wiping stock solution and waste liquid are randomly extracted from the plate wiping stock solution storage tank corresponding to the machine and the waste water outlet next to the machine respectively. In the laboratory in advance, place the evaporating dish in an oven at 105°C for 3 hours to keep the weight constant and record the weight. After mixing the extracted solution evenly, immediately use a 50ml pipette to extract two parts of the plate wiping stock solution and two parts of the waste liquid, respectively fill them in constant weight evaporating dishes, and use 1mol / l standard equivalent hydrochloric acid to titrate the plate wiping waste liquid to The pH value is 7±0.2, and the titration end point is indicated by a pH meter. Then add the same standard hydrochloric acid dropwise to the wiping stock solution until the pH value is 7±0.2.
[0021] After the test solution wa...
Embodiment 3
[0024] In the normal process printing state of the β gravure printing machine, randomly extract about 250ml of wiping stock solution and waste liquid from the wiping stock solution storage tank corresponding to the machine and the waste water outlet next to the machine respectively. In the laboratory in advance, place the evaporating dish in an oven at 105°C for 3 hours to keep the weight constant and record the weight. After mixing the extracted solution evenly, immediately use a 50ml pipette to extract 1 part of the plate wiping stock solution and 1 part of the waste liquid, respectively put them in constant weight evaporating dishes, and use 1mol / l standard equivalent hydrochloric acid to titrate the plate wiping waste liquid to The pH value is 7±0.2, and the titration end point is indicated by a pH meter. Then add the same standard hydrochloric acid dropwise to the wiping stock solution until the pH value is 7±0.2.
[0025] Evaporate the acid-added test solution to drynes...
PUM
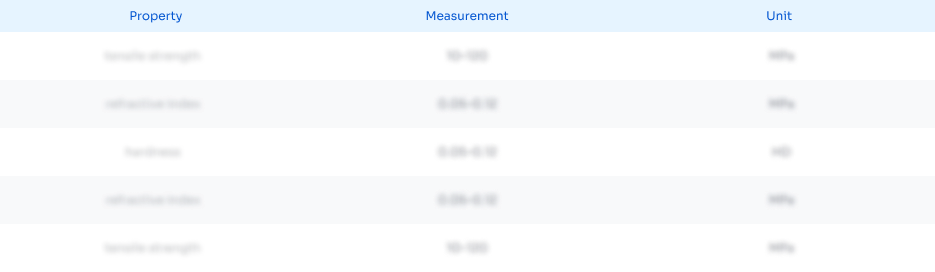
Abstract
Description
Claims
Application Information

- R&D
- Intellectual Property
- Life Sciences
- Materials
- Tech Scout
- Unparalleled Data Quality
- Higher Quality Content
- 60% Fewer Hallucinations
Browse by: Latest US Patents, China's latest patents, Technical Efficacy Thesaurus, Application Domain, Technology Topic, Popular Technical Reports.
© 2025 PatSnap. All rights reserved.Legal|Privacy policy|Modern Slavery Act Transparency Statement|Sitemap|About US| Contact US: help@patsnap.com