Method for producing pre-reducing composite sinter
A production method and technology for sintered ore are applied in the production field of pre-reduced composite sintered ore, which can solve the problems of high energy consumption, single charge structure, large investment in ore troughs, etc., so as to improve comprehensive grade, simplify blast furnace operation, and reduce bentonite. The effect of matching
- Summary
- Abstract
- Description
- Claims
- Application Information
AI Technical Summary
Problems solved by technology
Method used
Image
Examples
Embodiment 1
[0018] A production method of pre-reduced composite sintered ore, the method is to use high-basicity sintered ore and acid pellets to mix, and add coal powder to the raw material for making balls from acid pellets, and then mix them evenly The high-basic sinter and acid pellets are sintered together on the sintering machine to produce pre-reduced blast furnace charge. The method steps are:
[0019] ①Batching iron-containing raw materials, flux and fuel according to a certain proportion, and then mixing and granulating; wherein the weight ratio of each component is: iron-containing raw material 70, flux 27, fuel 3;
[0020] ②Batch iron concentrate, bentonite, and coal powder according to a certain proportion, and carry out mixing and pelletizing; wherein the weight ratio of each component is: iron concentrate 90, bentonite 1.5, coal powder 8.5; the particle size of the ball is 5-16mm.
[0021] ③ The raw materials prepared in step ① and the raw materials prepared in step ② are...
Embodiment 2
[0025] A production method of pre-reduced composite sintered ore, the method steps are:
[0026] ①Batching iron-containing raw materials, flux and fuel according to a certain proportion, mixing and granulating; wherein the weight ratio of each component is: iron-containing raw material 80, flux 14, fuel 6;
[0027] ②Batch iron concentrate, bentonite, and coal powder according to a certain proportion, and perform mixing and pelletizing; wherein the weight ratio of each component is: iron concentrate 80, bentonite 0.5, coal powder 19.5; the particle size of the ball is 5-16mm.
[0028] ③ The raw materials prepared in step ① and the raw materials prepared in step ② are batched according to the weight ratio of 3:2, mixed in a mixer, and then sent to a sintering machine for sintering.
Embodiment 3
[0030] A production method of pre-reduced composite sintered ore, the method steps are:
[0031] ①Batching iron-containing raw materials, flux and fuel according to a certain proportion, mixing and granulating; wherein the weight ratio of each component is: iron-containing raw material 75, flux 19, fuel 6;
[0032] ②Batch iron concentrate, bentonite, and coal powder according to a certain proportion, and carry out mixing and pelletizing; wherein the weight ratio of each component is: iron concentrate 85, bentonite 3, coal powder 12; the particle size of the ball is 5-16mm.
[0033] ③ The raw materials prepared in step ① and the raw materials prepared in step ② are batched according to the weight ratio of 4:1, mixed in a mixer, and then sent to a sintering machine for sintering.
[0034] In the above embodiments: iron-containing raw materials are selected from one or more of concentrate, rich ore powder, miscellaneous materials, and returned ore; the flux is one or more of lim...
PUM
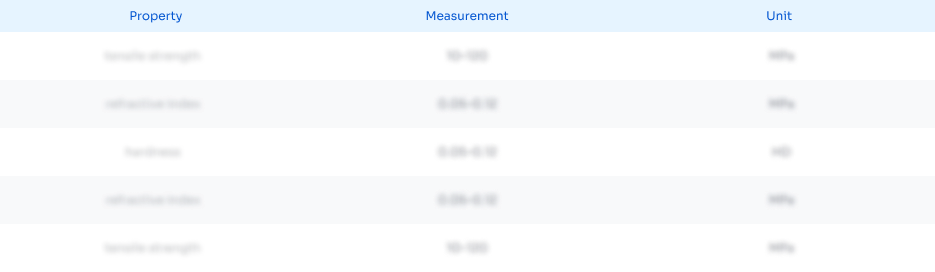
Abstract
Description
Claims
Application Information

- R&D Engineer
- R&D Manager
- IP Professional
- Industry Leading Data Capabilities
- Powerful AI technology
- Patent DNA Extraction
Browse by: Latest US Patents, China's latest patents, Technical Efficacy Thesaurus, Application Domain, Technology Topic, Popular Technical Reports.
© 2024 PatSnap. All rights reserved.Legal|Privacy policy|Modern Slavery Act Transparency Statement|Sitemap|About US| Contact US: help@patsnap.com