Nano layered calcium carbonate base bionic composite material and synthetic method thereof
A biomimetic composite material and nano-layered technology, which is applied in the treatment of calcium carbonate/strontium/barium, fibrous fillers, dyed low-molecular organic compounds, etc.
- Summary
- Abstract
- Description
- Claims
- Application Information
AI Technical Summary
Problems solved by technology
Method used
Image
Examples
Embodiment 1
[0026] Mix n-butylamine and calcium chloride at a mass ratio of 1:1, and dissolve it in water so that the mass ratio of calcium chloride to water is 0.0003:1, then add sodium carbonate, and make calcium chloride and sodium carbonate The molar ratio of the mixture is 1:1. After stirring for 0.5-1 hour, the mixture is transferred to a Teflon-lined reactor and heated in an oven at 80-200° C. for 6-20 hours. After the reaction, the reactor was taken out and cooled to room temperature naturally. Filter, wash with distilled water and ethanol, respectively, and dry at 80-120°C for 10-12 hours.
[0027] The obtained calcium carbonate complex is carried out X-ray diffraction (XRD) analysis, and the standard collection of illustrative plates of the XRD pattern of gained and calcium carbonate (Joint Committee Powder Diffraction Standard Card JCPDS: 47-1743) completely coincides, proves that prepared product Calcite-type calcium carbonate.
Embodiment 2
[0029] Mix n-butylamine and calcium chloride at a mass ratio of 3:1, and dissolve it in water so that the mass ratio of calcium chloride to water is 0.0003:1, then add sodium carbonate, and make calcium chloride and sodium carbonate The molar ratio is 1:1. After stirring for 0.5-1 hour, the mixture is transferred to a Teflon-lined reactor and heated in an oven at 80-200° C. for 6-20 hours. After the reaction, the reactor was taken out and cooled to room temperature naturally. Filter, wash with distilled water and ethanol, respectively, and dry at 80-120°C for 10-12 hours.
[0030] The obtained calcium carbonate complex is carried out X-ray diffraction (XRD) analysis, and the standard collection of illustrative plates of the XRD pattern of gained and calcium carbonate (Joint Committee Powder Diffraction Standard Card JCPDS: 47-1743) completely coincides, proves that prepared product Calcite-type calcium carbonate.
Embodiment 3
[0032] Mix n-butylamine and calcium chloride at a mass ratio of 5:1, and dissolve it in water so that the mass ratio of calcium chloride to water is 0.0003:1, then add sodium carbonate, and make calcium chloride and sodium carbonate The molar ratio is 1:1. After stirring for 0.5-1 hour, the mixture is transferred to a Teflon-lined reactor and heated in an oven at 80-200° C. for 6-20 hours. After the reaction, the reactor was taken out and cooled to room temperature naturally. Filter, wash with distilled water and ethanol, respectively, and dry at 80-120°C for 12 hours.
[0033] The obtained calcium carbonate complex is carried out X-ray diffraction (XRD) analysis, and the standard collection of illustrative plates of the XRD pattern of gained and calcium carbonate (Joint Committee Powder Diffraction Standard Card JCPDS: 47-1743) completely coincides, proves that prepared product Calcite-type calcium carbonate.
PUM
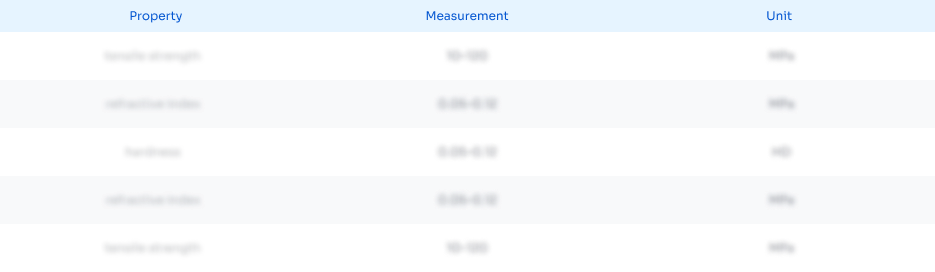
Abstract
Description
Claims
Application Information

- R&D
- Intellectual Property
- Life Sciences
- Materials
- Tech Scout
- Unparalleled Data Quality
- Higher Quality Content
- 60% Fewer Hallucinations
Browse by: Latest US Patents, China's latest patents, Technical Efficacy Thesaurus, Application Domain, Technology Topic, Popular Technical Reports.
© 2025 PatSnap. All rights reserved.Legal|Privacy policy|Modern Slavery Act Transparency Statement|Sitemap|About US| Contact US: help@patsnap.com