Multi-joint flexible mechanical arm
A flexible robotic arm and multi-joint technology, applied in the field of flexible robots, achieves the effect of achieving flexibility, large flexibility, and high load-to-weight ratio
- Summary
- Abstract
- Description
- Claims
- Application Information
AI Technical Summary
Problems solved by technology
Method used
Image
Examples
Embodiment Construction
[0018] The present invention will be further described below in conjunction with drawings and embodiments.
[0019] In the embodiment shown in FIG. 1 , the entire robotic arm is composed of a base 1 and five joint modules connected in series, and each joint module is composed of a torsion joint 2 and a bending joint 3 . The power comes from the motor on the base 1, and the motion of the motor is transmitted to the bending joint 3 through the torsion joint 2. Adding the same joint module at the end of the manipulator can expand the length and degree of freedom of the manipulator.
[0020] As shown in Fig. 2A, Fig. 2B, and Fig. 2C, the torsional joint includes a torsional input reversing gear set, a torsional clutch set, a torsional output reversing gear set, a torsional reducer, a torsional driving arm and a spur gear planetary gear train; the torsional input The reversing gear set is composed of twisting input central gear 6, twisting left reversing gear 4, twisting overwheel ...
PUM
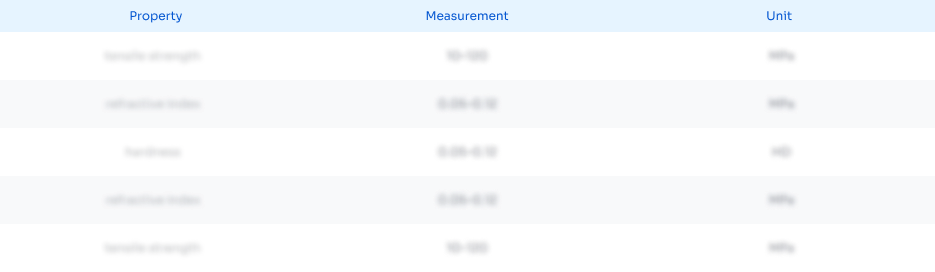
Abstract
Description
Claims
Application Information

- R&D
- Intellectual Property
- Life Sciences
- Materials
- Tech Scout
- Unparalleled Data Quality
- Higher Quality Content
- 60% Fewer Hallucinations
Browse by: Latest US Patents, China's latest patents, Technical Efficacy Thesaurus, Application Domain, Technology Topic, Popular Technical Reports.
© 2025 PatSnap. All rights reserved.Legal|Privacy policy|Modern Slavery Act Transparency Statement|Sitemap|About US| Contact US: help@patsnap.com