Process for producing rigid polyurethane foam
A technology of rigid polyurethane and manufacturing methods, applied in the field of rigid polyurethane foam, can solve the problems of small thermal conductivity, fragility and low thermal conductivity, and achieve excellent dimensional stability, excellent adhesion, and thermal conductivity The effect of less deterioration
- Summary
- Abstract
- Description
- Claims
- Application Information
AI Technical Summary
Problems solved by technology
Method used
Image
Examples
Embodiment
[0065] Hereinafter, the present invention will be specifically described based on examples, but the present invention is not limited thereto. In addition, in this embodiment, the performance of the panel foam is cited as a preferred example, but the use of the rigid polyurethane foam prepared by the method of the present invention is not limited to the panel foam application.
[0066] The properties of the panel foams shown in Comparative Examples 1 to 3 and Examples 1 to 3 described later were produced and measured in the following procedures. Inner volume 500cm 3 Add the respective ingredients based on the quality of the recipe to a paper cup, mix well to achieve uniformity, and make a premix. Adjust the stock solution temperature of the premix solution to 20°C. Next, pour in Mirionet MR-200 manufactured by Nippon Polyurethane Industry Co., Ltd. as a polymeric isocyanate, which has been preliminarily adjusted to a stock solution temperature of 20°C, and stir at a rotation ...
Embodiment 1
[0104] The formulation (12) in Example 1 shown in Table 4 is based on 5.50 parts of water, 0.61 parts of TMHDA, and Toray Dow Corning for 100 parts of Toho Polyol TE-280 manufactured by Toho Chemical Industry Co., Ltd. 1.5 parts of SZ-1718 manufactured by (former Japan Unica Company) and 197.0 parts of Mirionet MR-200 manufactured by Japan Polyurethane Industry Co., Ltd. are mixed to make the total mass 300g. 100 parts of Dongbang Polyol AN-280 manufactured by Industrial Co., Ltd. are mixed according to the comparison of 5.36 parts of water, 1.04 parts of TMHDA, 1.5 parts of SZ-1718, and 189.7 parts of MR-200, so that the total mass is 300g; formula (14) For 100 parts of Toho Polyol XE-280 produced by Toho Chemical Industry Co., Ltd., mix in proportions of 4.36 parts of water, 1.04 parts of TMHDA, 1.5 parts of SZ-1718, and 189.7 parts of MR-200, so that the total mass is 300g, formula (15) is relative to Dongho Polyol NE-310 manufactured by Toho Chemical Industry Co., Ltd., mi...
Embodiment 2
[0107] Formulation (16) in Example 2 shown in Table 5 is 5.60 parts of water, 1.09 parts of TMHDA, Toray Dou Corning for 100 parts of Toho Polyol AE-270 manufactured by Toho Chemical Industry Co., Ltd. 1.5 parts of SZ-1718 manufactured by (former Japan Unica Company) and 203.1 parts of Mirionet MR-200 manufactured by Japan Polyurethane Industry Co., Ltd. are mixed to make the total mass 300g. 100 parts of Toho Polyol AE-320 manufactured by Industrial Corporation, mixed in the ratio of 5.15 parts of water, 1.00 parts of TMHDA, 1.5 parts of SZ-1718, and 178.2 parts of MR-200, so that the total mass is 300g; formula (18) For 100 parts of Toho polyol AE-370 manufactured by Toho Chemical Industry Co., Ltd., mix in proportions of 4.78 parts of water, 0.53 parts of TMHDA, 1.5 parts of SZ-1718, and 158.9 parts of MR-200, so that the total mass is 300g; Prescription (19) is relative to 100 parts of Toho Polyol AB-372 manufactured by Toho Chemical Industry Co., Ltd., mixed in a ratio of...
PUM
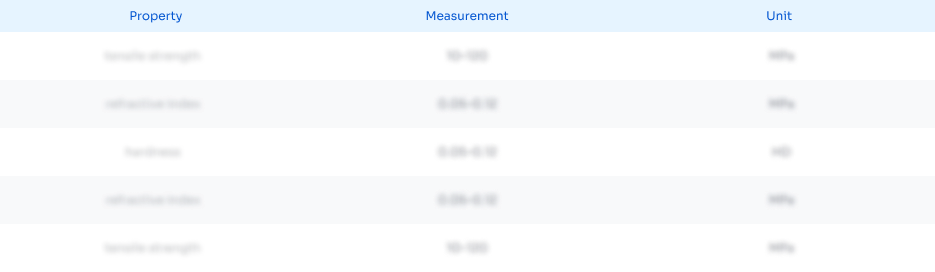
Abstract
Description
Claims
Application Information

- R&D
- Intellectual Property
- Life Sciences
- Materials
- Tech Scout
- Unparalleled Data Quality
- Higher Quality Content
- 60% Fewer Hallucinations
Browse by: Latest US Patents, China's latest patents, Technical Efficacy Thesaurus, Application Domain, Technology Topic, Popular Technical Reports.
© 2025 PatSnap. All rights reserved.Legal|Privacy policy|Modern Slavery Act Transparency Statement|Sitemap|About US| Contact US: help@patsnap.com