Force balancing resonance micro-mechanical gyro
A technology of micro-mechanical gyroscope and force balance, which is applied in the direction of speed measurement by gyro effect, gyroscope/steering sensing equipment, measuring device, etc., which can solve the problems of insufficient sensitivity and resolution of micro-mechanical gyroscope
Inactive Publication Date: 2010-11-10
BEIHANG UNIV
View PDF0 Cites 2 Cited by
- Summary
- Abstract
- Description
- Claims
- Application Information
AI Technical Summary
Problems solved by technology
The technical problem of the present invention is: to overcome the deficiencies of the prior art, to provide a force-balanced resonant micro-machined gyroscope, to solve the existing micro-machined gyroscope sensitivity, resolution is not high enough, and the problems existing in capacitance detection, suppress non- linear effect
Method used
the structure of the environmentally friendly knitted fabric provided by the present invention; figure 2 Flow chart of the yarn wrapping machine for environmentally friendly knitted fabrics and storage devices; image 3 Is the parameter map of the yarn covering machine
View moreImage
Smart Image Click on the blue labels to locate them in the text.
Smart ImageViewing Examples
Examples
Experimental program
Comparison scheme
Effect test
Embodiment Construction
the structure of the environmentally friendly knitted fabric provided by the present invention; figure 2 Flow chart of the yarn wrapping machine for environmentally friendly knitted fabrics and storage devices; image 3 Is the parameter map of the yarn covering machine
Login to View More PUM
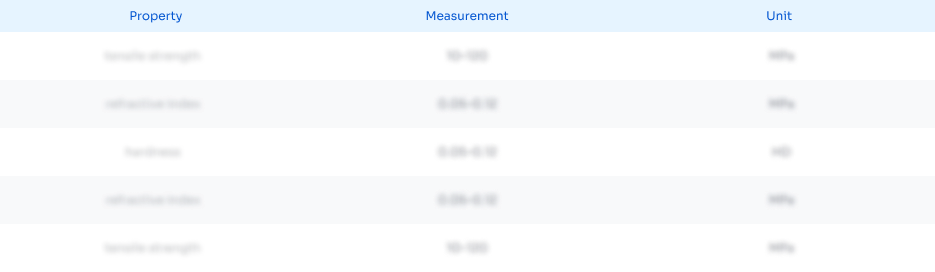
Abstract
The invention relates to an equilibrium type resonance micro mechanical top, which includes static comb tooth driver, mass block, double end tuning fork resonator and static comb tooth strength balancer. When adds the driving voltage to the static comb tooth driver, the mass block does along x axis direction oscillation motion, and circles the z axis in exterior under the rate of angular motion function to produce along y direction coriolis force. The static comb tooth strength balancer used to balance the mass block in y direction Coriolis force and keep the mass block in the equilibrium position of the y direction. The invention structural style enhanced the micro mechanical top sensitivity, the resolution and the dynamic range and realized Coriolis force change, which had the top sensitive angular speed to transform the resonator resonance frequency change, and then through the feedback return route adjustment achieved the new balanced equilibrium type feedback system, and effectively suppressed the non-linear influence.
Description
Force Balanced Resonant Micromachined Gyroscope technical field The invention belongs to the field of micro-mechanical sensors in micro-electro-mechanical systems (MEMS), and is widely used in the fields of automotive electronics, aerospace, weaponry and the like as a micro-inertial device. Background technique The classic frame-type mechanical rotor gyroscope based on the principle of angular momentum is assembled from hundreds of (about 300) parts. It has a complex structure, large volume, and short service life, which cannot meet the requirements of technological development and many new applications. Therefore, solid-state gyroscopes without mechanical rotors have been developed one after another, such as laser gyroscopes, hemispherical resonant gyroscopes, and fiber optic gyroscopes. The performance of the first two gyroscopes can reach the drift accuracy of inertial navigation (0.01° / h); but the price is high and the volume is large, which is still not suitable for t...
Claims
the structure of the environmentally friendly knitted fabric provided by the present invention; figure 2 Flow chart of the yarn wrapping machine for environmentally friendly knitted fabrics and storage devices; image 3 Is the parameter map of the yarn covering machine
Login to View More Application Information
Patent Timeline

Patent Type & Authority Patents(China)
IPC IPC(8): G01C19/56G01C19/5621
Inventor 樊尚春王莹莹蔡晨光
Owner BEIHANG UNIV
Features
- R&D
- Intellectual Property
- Life Sciences
- Materials
- Tech Scout
Why Patsnap Eureka
- Unparalleled Data Quality
- Higher Quality Content
- 60% Fewer Hallucinations
Social media
Patsnap Eureka Blog
Learn More Browse by: Latest US Patents, China's latest patents, Technical Efficacy Thesaurus, Application Domain, Technology Topic, Popular Technical Reports.
© 2025 PatSnap. All rights reserved.Legal|Privacy policy|Modern Slavery Act Transparency Statement|Sitemap|About US| Contact US: help@patsnap.com