Internal recycling drying machine of rubber raw materials
A rubber raw material, internal circulation technology, applied in progressive dryers, dryers, drying solid materials, etc., can solve the problems of difficult to guarantee material quality, high heat consumption, high operation and maintenance costs, and achieve the effect of reducing cost.
- Summary
- Abstract
- Description
- Claims
- Application Information
AI Technical Summary
Problems solved by technology
Method used
Image
Examples
specific Embodiment approach 1
[0007] Specific Embodiment 1: This embodiment is described with reference to FIGS. 1 to 8. This embodiment consists of a box body 1, a frame 2, a feed drive device 9, a discharge drive device 10, a raw material conveyor belt, a baffle plate 16, a motor 17, The fan 18, the heat exchanger 20, the upper temperature measuring device 21, and the lower temperature measuring device 22 are composed; the box body 1 is divided into the first drying chamber 3, The second drying chamber 4, the third drying chamber 5, the fourth drying chamber 6, the fifth drying chamber 7, and the cooling chamber 8, the front of the first drying chamber 3 is provided with a feeding drive device 9, and the rear of the cooling chamber 8 A discharge drive device 10 is provided, and the feed drive device 9 is in transmission connection with the discharge drive device 10 through the raw material conveyor belt passing through the box body 1. The upper end surface of the fifth drying chamber 7 and the upper end s...
specific Embodiment approach 2
[0008] Specific embodiment two: this embodiment is described in conjunction with Fig. 1 and Fig. 2, the discharge driving device 10 of this embodiment is made up of rear frame 24, driven pulley 13, driven shaft 14; Described rear frame 24 is fixed on On the ground, driven shaft 14 is housed on rear frame 24, and driven pulley 13 is housed on driven shaft 14. With such arrangement, the structure is simple, the transmission is reliable, and it is easy to install and manufacture. Other components and connections are the same as those in the first embodiment.
specific Embodiment approach 3
[0009] Specific embodiment three: this embodiment is described in conjunction with Fig. 1 and Fig. 2, the feeding driving device 9 of this embodiment is made up of front frame 23, driving shaft 12, driving pulley 11; Said front frame 23 is fixed on the ground On, drive shaft 12 is housed on the front frame 23, and driving pulley 11 is housed on the driving shaft 12, and driving pulley 11 is connected with passive pulley 13 transmissions by raw material conveyor belt. With such arrangement, the structure is simple, the transmission is reliable, and it is easy to install and manufacture. Other compositions and connections are the same as those in Embodiments 1 and 2.
PUM
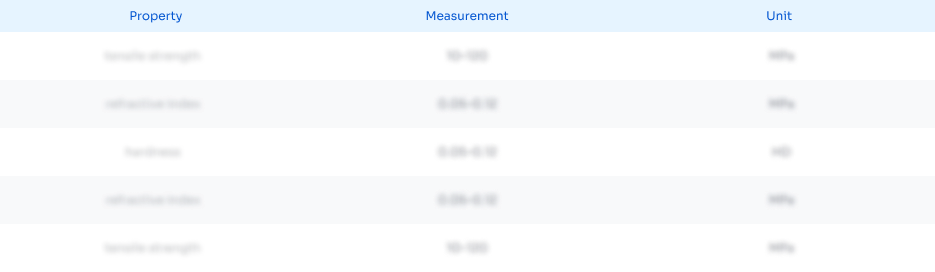
Abstract
Description
Claims
Application Information

- R&D
- Intellectual Property
- Life Sciences
- Materials
- Tech Scout
- Unparalleled Data Quality
- Higher Quality Content
- 60% Fewer Hallucinations
Browse by: Latest US Patents, China's latest patents, Technical Efficacy Thesaurus, Application Domain, Technology Topic, Popular Technical Reports.
© 2025 PatSnap. All rights reserved.Legal|Privacy policy|Modern Slavery Act Transparency Statement|Sitemap|About US| Contact US: help@patsnap.com