Bamboo slicer
A slicing machine and bamboo chip technology, which is applied in mechanical equipment, veneer manufacturing, sugarcane machining, etc., can solve problems such as affecting the number of split bamboo chips, increasing production costs, and wasting resources.
- Summary
- Abstract
- Description
- Claims
- Application Information
AI Technical Summary
Problems solved by technology
Method used
Image
Examples
Embodiment Construction
[0011] The serial numbers in the figure indicate respectively: telescopic rod 1, side wall panel 2, strip guide plate 3, blade 4, pressing piece 5, adjusting screw 6, spring 6a, front roller 7, rear slider 8, chute 8a, rear roller 9 , gear 10, sprocket 11, chain 11a, inlet 12, gear 13, pulley 14, belt 15, frame 16, motor output shaft 17, motor 18, belt 19, eccentric shaft 20, eccentric wheel 21, swing rod 22, Small bearing 23, fixed seat 24, adjusting nut 24a, fork shaft 24b, strip guide plate 25, spring 26,
[0012] In Fig. 1, the transverse structure of the upper part of the entire frame 16 is roughly in a concave shape. When viewed from the right, the right side of the concave part is the inlet 12 for conveying bamboo chips. , to ensure that the bamboo slices enter the roller gap in a horizontal state and meet the knife edge, and the bamboo slices are placed and conveyed in a single thickness. The bamboo sheet conveying device is located in the middle part of the concave p...
PUM
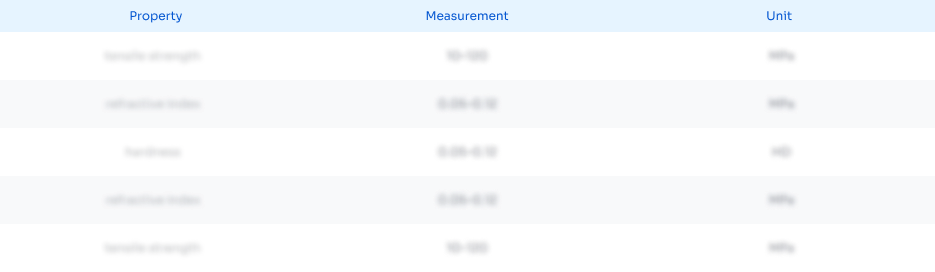
Abstract
Description
Claims
Application Information

- Generate Ideas
- Intellectual Property
- Life Sciences
- Materials
- Tech Scout
- Unparalleled Data Quality
- Higher Quality Content
- 60% Fewer Hallucinations
Browse by: Latest US Patents, China's latest patents, Technical Efficacy Thesaurus, Application Domain, Technology Topic, Popular Technical Reports.
© 2025 PatSnap. All rights reserved.Legal|Privacy policy|Modern Slavery Act Transparency Statement|Sitemap|About US| Contact US: help@patsnap.com