Production method of short staple enveloped composite yarn
A production method and composite yarn technology, applied in the field of spinning, can solve the problems of raw material selection, product application field limitations, affecting fabric dyeing and wearing performance, and high production costs
- Summary
- Abstract
- Description
- Claims
- Application Information
AI Technical Summary
Problems solved by technology
Method used
Image
Examples
Embodiment
[0020] In order to verify the wrapping effect and optimize the process parameters, natural colored cotton and polyester staple fiber are used to produce 20 wrapping composite yarns. The colored cotton is used as the outer fiber and the polyester staple fiber is the core yarn. The yarn weight ratio is 50% of the colored cotton. , Polyester staple fiber accounts for 50%. First press the colored cotton and polyester staple fiber separately figure 1 The process flow produces roving, and then produces wrapping composite yarn on the modified spinning device. The process parameters of the machine are configured as follows: the twist is 73 twists / 10cm, the front roller speed is 190r / min, and the front and rear roller gauge is 19×29mm ; There is no difference between the number of broken ends per thousand spindles and conventional varieties in the production process. The spinning is smooth and the quality is stable. The quality indicators are shown in the following table:
[0021] ...
PUM
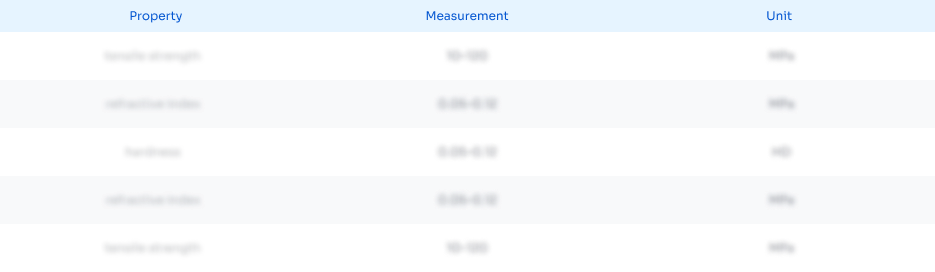
Abstract
Description
Claims
Application Information

- R&D
- Intellectual Property
- Life Sciences
- Materials
- Tech Scout
- Unparalleled Data Quality
- Higher Quality Content
- 60% Fewer Hallucinations
Browse by: Latest US Patents, China's latest patents, Technical Efficacy Thesaurus, Application Domain, Technology Topic, Popular Technical Reports.
© 2025 PatSnap. All rights reserved.Legal|Privacy policy|Modern Slavery Act Transparency Statement|Sitemap|About US| Contact US: help@patsnap.com